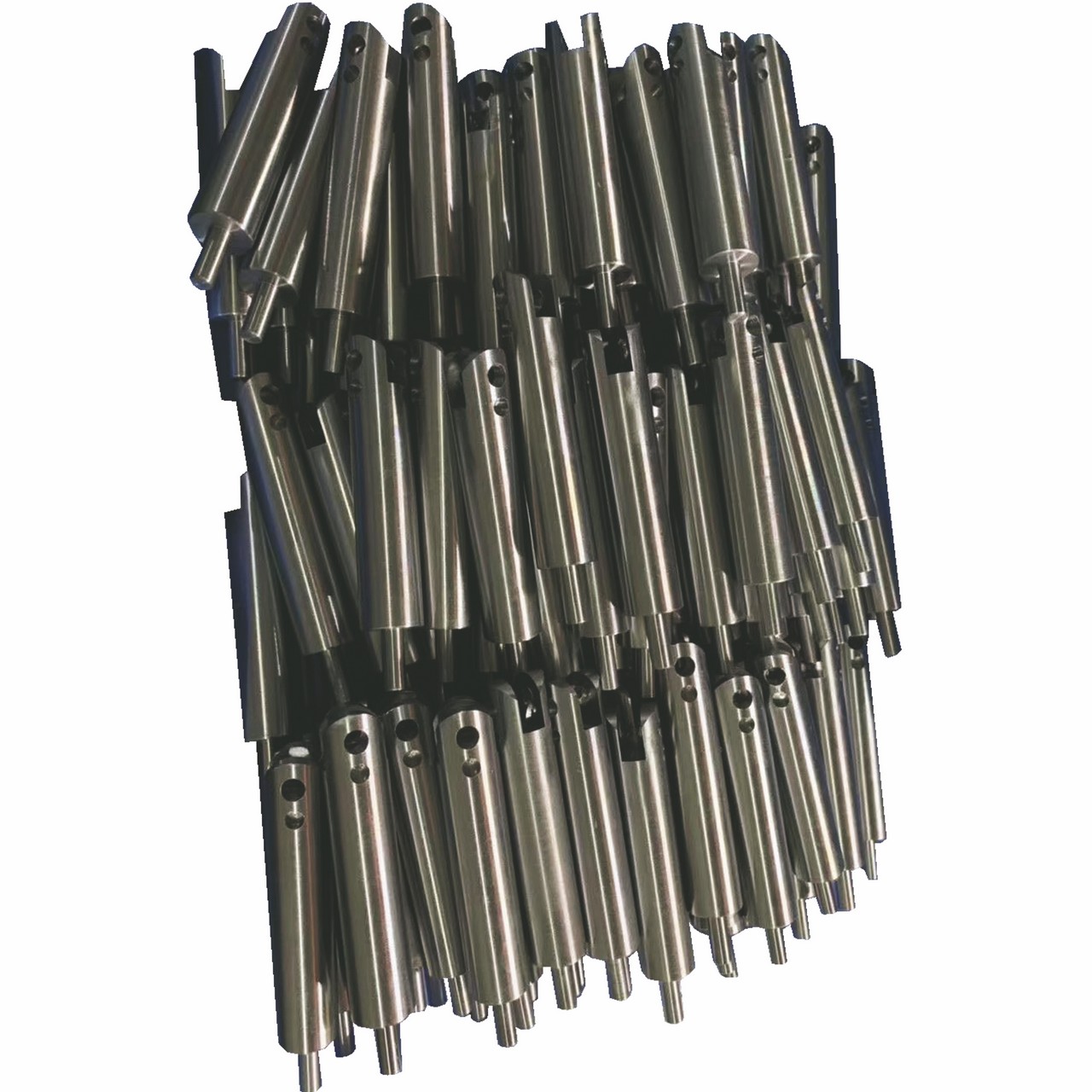
COMPUTER NUMERICAL CONTROL turning is one of the most significant strategies of producing. It will produce cylindrical parts with assorted contours.
In machine building, you can't bypass shafts to broadcast power from your motor towards the moving parts. Shafts, needless to say, require turning. But COMPUTER NUMERICAL CONTROL turning and boring find lots of use in several industries to create usually axi- symmetric parts.
Dining tableof Articles hide
I What exactly is Resorting?
2CNC Turning Process
a fewTurning Parameters
4CNC Lathe Main Parts
VersusForms of Lathes
MireAxis Identification in CNC Lathe
VII Different Businesses
VIII Suitable Materials for Resorting
IX Conclusion
What's Resorting?
Turning is really a subtractive engineering process that runs on the reducing tool to get rid of material for producing cylindrical parts. The tool itself progresses the axis in the machined part as the part is rotating, making a helical toolpath.
The definition of turning means producing parts by cutting forms of procedures around the external surface. Another of turning is boring, through which lathe machines are utilized for making hollow parts, as an example.
The firstlathe machine is in the past one of the initial available for producing parts within a semi- built to fashion. Today, typically provide CNC turning services. Which means that the procedure is usually automated from start to surface finish.
CNC describes computer statistical control, meaning computerised systems alleviate the machinery. The input is digital code. These controls most of the tool moves and speed for spinning along with other supporting behaviours like utilization of coolant.
Personal computerNUMERICAL CONTROL Turning Strategy
What really does the turning process actually includes? If the cutting itself is extremely straightforward, we will go through the whole pattern here that actually starts from developing a CAD file.
Steps of the method are:
Developing a digital representation of the business in CAD
Leading toinside the machining code from your CAD files
Computer numerical controllathe setup
Producingfrom the converted parts
CAD design& G code
The initial 2 steps is visible separate or going hand- in- hand. A proven way is just to utilize a CAD program for the files and send them into production. The manufacturing manufacture will create the G code plus the M matrix for that machining job.
CAD- CAM for turning operationsCAD- CAM for turning businesses
Alternative methods is in order to use CAD- CAM software which lets the structure engineer test the producibility of the business. The completepowerful simulation tools can consider the entire process from organic material to the last product, even utilizing the input regarding finishing requirements.
Lastly, gleam manual way for resulting in the code. As an example, it is possible to automatically generate the matrix from the 2D drawing, losing sight of you with 2 options– either writing the code physically or assembling a 3D model first.
Your powerful CAM programs might not necessarily get everything spot- on, so looking at the coded instructions is inspired.
Lathe setup
Next comes the device setup. That is where the device operator 's role becomes evident. Although modern CNC lathes do a lot of the work automatically, the operator still plays a essential part.
Practices for developing a COMPUTER NUMERICAL CONTROL turning centre:
Making certain the ability is crooked. CNC engineering could be dangerous, so extra care is essential and looking at the power-switch is the cornerstone because of this.
Securing the business in to the chuck. The businesstoss holds the business throughout the whole process. Improper loading can both pose dangers in addition to cause a accomplished do minus the wrong dimensions.
Filling the tool turret. Turning contains many steps, so make for certain to select the right tooling for a particular finish. The turret can take many tools simultaneously for any unlined procedure from continue steadily to finish.
Tuned. Both tool and part need to be set up correctly . Only if anything is misaligned, the consequence won't match the requirements.
Publish this system. The final step before pushing the commencement button is uploading the code towards the CNC machine.
Componentformation
Computer numerical controlsubmiting productionCNC spinning in production
The ultimate way to get the utilization of producing is merely watching it above. You can observe both turning and boring within this video. The commonestraw information, as evident, just isn't a round bar which is the commonest option. Rather, a hexagonal profile is the more effective strategy to use here in order to avoid CNC milling down the road.
With regards to the complexness of the business enterprise, a number of cycles might be necessary. Cycle time calculations determine your final time spent which is required for cost calculations. A spinning cycle time contains:
Packing time. We already described it included in the create but a cycle may warrant yet another way of loading the business into the machinery.
Cutting time. Enough time it should take depends in regards to the cut depth and offer rate.
Idle time. Idles times make reference to whatever is not cutting, example process of tools from the piece, changing the adjustments in the lathe, etc.
Instrument lifetime. Although each cycle does indeed not need replacing the tool completely, the cutting time will be taken into consideration instead of the overall life long an instrument to add it in one last cost.
Get the material fabrication quote in seconds
to ensure
Quotationin seconds
symbol
Quicklead times
image
Shippingby Fractory
Obtainquote
SwitchingDetails
The parameters of CNC resorting count on various aspects. All these generally include the items of the business and tool, tool size, finishing requirements, etc.
The key parameters for CNC turning are:
Spindle speed. Lightweight rotations each and every minute( rpm) also it shows the rotational acceleration from the spindle( N), thus also the workpiece. The spindle speed is within direct link with all the cutting speed which also takes the diameter in mind. Therefore, the spindle speed should vary to keep a reliable cutting speed if the peak changes considerably.
Workpiece diameter. While said, this plays an natural part to travel to the best cutting speed. The is D and the machine is mm.
Cutting speed. The equation for calculating the reducing speed is V= πDN/1000. It shows the relative speed in the workpiece for the cutting tool.
Feed rate. Lightweight mm/ rev plus the symbol is s. Cutting feed shows the exact distance the cutting tool goes per one time for the workpiece. The length is tested axially.
Axial cut depth. Very self- explanatory because it shows the depth of any cut inside the axial course. It is the principal variable for facing operations. A greater feed rate puts more stress on the cutting tool, reducing its lifetime.
Radial cut increased detail. Another of axial cut, it shows the depth of reducing perpendicular towards the axis. All over again, lower feed rates help lengthen the time of tools and secure the conclusion.
PcNUMERICAL CONTROL Lathe Main Parts
Now, let 's see the principal the some other part of a turning centre.
Headstock
The leadingheadstock of the CNC lathe evens up leading area of the device. That is where the driving motor is over the mechanisms to power the spindle.
The chuck or collet links for the spindle. Either of those, in exchange, holds the workpiece through the turning operation.
Throwand collet
The chuck side handles the machined part by it really is jaws. It attaches straight to the spindle but is they are merely, so different sized parts could be machined.
Collet is basically a compact version of any toss. The business enterprise size well suited for collets is about 70 mm. They supply a far greater grip for bits.
Tailstock
Another finish of any CNC turning centre. Some tailstock attaches straight to your bed and its own purpose is to offer support longer components. The tailstock quill offers the support by hydraulic force.
The businesspower still arises from the spindle plus the tailstock just runs with the business. Utilizing a tailstock just isn't suitable when face turning is important, as it'll be when it comes to.
Lathe bed
The pickup bed is only a base zone that engraves the bench, supporting other machine parts. The carriage runs on the crib which can be heat- medicated to confront the machining effects.
Buggy
The buggy engraves ways for falling alongside the spinning workpiece. The theory keeps the equipment, permitting cutting process to take place.
Turret gungun
Newer machines typically appear with a turret that replaces the carriage. They holds more tools at precisely the same time , the switching from just one method to another half the normal commission of times - drinking.
Residetooling having a CNC machineLive tooling over a CNC machine
CNC machining centres includes live tooling. While single point cutting tools are perfect for most turning operations, live tooling means mills, drills as well as other tools which acquire own power. Allowing creating keyways or holes perpendicular to the business axis without needing various other machinery in the act .
Impactpanel
That's where computer numerical control kicks in. The brains of CNC turning machines are only behind the snowboard. This programpanel itself allows the operator to change this system and begin it.
Kinds of Lathes
An array of CNC lathes provides a number of possibilities. Each includes a unique pair of features although are far more automated than others. So everything experience it is place, in the event the few one- off jobs at just a little machine shop or order production for larger quantities.
Seatslathe
Title means it is small enough for connecting it to some tailored workbench. So many people are , still, bigger than small or mini- lathes.
Some good way to execute normal machining or a particular tool for any hobbyist, it can handle doing much of the mandatory businesses. A bench lathe needs a skilful machinist as there's almost no automation, getting decidedly more responsibility within the agent.
Powerplantlathe
The most frequent form of lathe. Its name has stuck because the nineteenth century whenever a steam engine unit try this specimen stand away in the middle of other manual lathes. Because the kick off point from the 20th century, a conversion towards electric motors became coming .
Using gearboxes inside the headstock made picking out spindle speed simple high- speed machine tools became typical. The current- found power pushed the to invent innovative ways of accelerating the tool life. Replaceable carbide inserts were just the way to accomplish this .
Consequently , engine lathes is capable of doing CNC machining at high speeds, contributing to shortened formation times and spend less. Although still common in workshops, engine lathes laid the building blocks for increased performance as well as the automation of machining.
Toolroom lathe
Exactly like the motor engine lathe by differences. Usually, they're more compact in size to fit right in tighter spaces. At precisely the same time , there are a few extra abilities available, that makes it rather a greater- complete machine, not merely one perfect for entry- level.
The toolroom lathes include chuck and collets, taper attachment and a lot more that, for instance, simpler counter lathes would not have .
Turret gungun and capstan lathes
These kind of lathes are virtually interchangeable in line with the methods they is able to do. When you learned before, conditions turret brings a variety of automation possibilities. Also, additional procedures can be carried out for a passing fancy workbench.
From making and boring to drilling, threading and making keyways, everything is achievable with out a change of tools. The requiredturret holds all the mandatory tooling simultaneously, so you can just go in a single process to another .
Joining CNC with less manual jobs, producing almost identical machined parts in batches is a powerful- point of the sort of lathes.
Multispindle lathe
Also referred to as mess machines, the multispindle lathe has greater than a single spindle. The additional capacity is very well suited for high- volume creation.
There's also smaller variations of those machines, called mess machines. Also, larger machines are referred to as chuckers.
Creating the equipment requires lots of time, and so the combination of this and the very high cost the device itself needs high- quantity production to pay it back . When applying this, they can make similar parts with superior, low cycle times and almost no manual work besides the original setup.
So large- batch manufacturing can considerably lower the price tag on CNC engineering.
Cnc-lathe
Even though some of these types also support a CNC system, the pc NUMERICAL CONTROL lathe deserves a different mention.
CNC describes computer statistical control, which manages operating the equipment to some extent . This type of is dependent upon the precise equipment, as they may be completely or semi- automatic.
Partial- automated CNC lathes require a tad bit more work from the device operator whereas completely automated centres are capable of doing from mounting the workpieces to changing the equipment.
The tophighly accurate CNC machines are the top the current industry is offering . Digitising the whole process from your creation of CAD to a totally finished part is achievable. Also, the enclosures significantly reduce steadily the risk during machining, like employees are certainly not subjected to any moving components, controlling anything necessary from a monitor.
Axis Recognition in CNC Lathe
Computer numerical controllathe axes
The most typical method of identifying the axes on a conventional CNC lathe machine goes that way:
The Unces axis runs parallel towards the axis within the workpiece. Which means tool can move over the part of the items whilst the part is revolving round the Z axis( C). Motion across the Z axis decides the entire job.
As you can plainly see , the X axis is perpendicular for the Z axis. Therefore, the tool can move from the piece around the X axis to look for the diameter of the company.
DifferentOperations
CNC turning is ideal for executing a range of operations. Many of us have named a number of them already but let 's possess a nearer look now to get clearness to the talents of lathe machines.
Lathing operationsLathing operations
Altering
The most frequent operation. An individual- point tool moves across the axis in the workpiece to get rid of material from the company surface. It will produce various contours, like steps, tapers, etc . Normally, several passes attained to ultimately achieve the finish effect.
Due to the high accuracy attainable with turning, the constraints and fits are often chosen on the hole- simplest system. Attaining the tight tolerances with CNC turning is easier than carrying it out same when going a hole.
Going through
Facing removes a layer of fabric from the final in the workpiece. Usually, the point is to realize an acceptable surface finish. Because the cutting interesting depth won't have to be very deep, an individual pass is capable of doing that. The movement from the cutting tool is verticle with regards to the spinning axis.
Grooving
Much like facing, the tool moves perpendicularly for the rotating axis. As opposed to cutting the conclusion from the workpiece, grooved cutting is conducted somewhere down the medial side. An individual point turning tool is able to do the cut in one single pass, in the event the width from the cut is identical towards the tool 's size. Otherwise, multiple cuts attained.
Separating
Parting is also called removing. The last option term describes this turning process in an exceedingly straightforward manner. The method itself appears like grooving nevertheless the cutting tool will reach the axis of the business. Meaning it slashes off a segment of the business.
Threading
Here we remain discussing an exterior operation. So threading is accustomed to cut threads on top of part. The specifics from the thread may be configured and achieving the end result may require several goes on.
Going
The initial internal process upon this list. When talking about traditional turning, drilling can be executed on the conclusion in the workpiece, close to the axis. As the business is content spinning anyway, the tool bit can remain stationary. Newer CNC lathe centres may use live tooling for producing perpendicular holes on the perimeters or elsewhere.
Boring
The contrary of turning. Exactly the same features can be carried out , just on the liner surface. Boring requires some drilling first, to make space for inserting the equipment in to the workpiece. Following that, enlargening the opening with single point cutters can be done, along side adding steps, chamfers, etc.
Reaming
Reaming is just a machining process whereby a multi- toothed fluted tool enters a preexisting hole to really make it bigger. The end result has an incredibly soft surface finish with tight anatomist tolerances. The task itself appears just like drilling from the beginning .
Gently tapping
Similar to reaming, needs a previously drilled pit. A faucet enters the present hole presenting it an internal thread. Requirements for the present hole are linked to the thread size– it ought to be alongside to the end in the thread teeth.
AppropriateMaterials for Resorting
Besides the kinds of lathes we described earlier, there are many categories based on the proper materials for any lathe. Wood, metal and goblet all will vary lathes simply because they each need some specific attributes, in addition to cutting velocities.
In terms of material profile, square, spherical, hexagonal, etc. are welcome. Seeing among the videos above shows, having profiles besides round is useful if your final part just isn't round in the slightest sections.
Suitable materials for turning include:
Metallic
Genuinewood
A glass
Plastic-type- type material
Wax, etc.
Laptop or computer Numerical Control (CNC) machining is a manufacturing process through which pre-programmed computer software dictates the activity of factory tools and machinery. Typically the process enables you to control a range of complex machinery, from grinders and lathes to mills and CNC routers. Having CNC machining, 3d cutting tasks can be accomplished in a single pair of prompts.
The COMPUTER NUMERICAL CONTROL process runs compared with -and thus supersedes- the constraints of handbook control, where live operators are needed to prompt and guide the directions of machining tools via levers, keys and wheels. For the onlooker, a COMPUTER NUMERICAL CONTROL system might appear like a regular collection of computer components, but the programs and consoles utilized in CNC machining recognize it from all the other varieties of computation.
Will need to you be considering utilizing CNC making to produce various products, find out and about more about how precisely CNC engineering and CNC coding works. You might also keep asking about the key types of CNC machines and the sort out of it can do to verify that it can be practical.
Precisely how Does CNC Engineering Work
When a CNC system is activated, the specified slices are programmed into the software and dictated to matching tools and machines, which carry out and about the dimensional responsibilities as specified, much like a automaton.
In CNC coding, the code power generator within the statistical system will usually expect mechanisms are faultless, despite the likelihood of errors, which is greater each time a CNC machine is directed to lower much more than one direction all together. The placement of an tool in a numerical control method is outlined by a group of inputs known as the part program.
With a numerical control machine, programs are put via punch charge cards. By contrast, the programs for COMPUTER NUMERICAL CONTROL machines are provided to computers through small keyboards. COMPUTER NUMERICAL CONTROL programming is stored in a computer’s memory. The passcode itself is written and edited by programmers. Therefore, COMPUTER NUMERICAL CONTROL systems offer a long way more expansive computational capacity. Moreover, COMPUTER NUMERICAL CONTROL systems are by no means stationary since newer requires can be included to pre-existing programs through revised passcode.
CNC Machine Coding
In CNC making, machines are controlled via numerical control, wherein an use program is given to control an object. Chinese guiding CNC machining is alternately labelled as G-code, and it’s written to control the many behaviors of a corresponding machine, including the speed, give rate and skill.
Basically, CNC engineering makes it possible to pre-program the speed and position of machine tool functions and run them via software in repetitive, foreseen cycles, all with little involvement from human operators. Inside the CNC machining process, a 2D or 3D CAD painting is conceived, which is then converted to computer passcode for the COMPUTER NUMERICAL CONTROL system to do. Following your program is inputted, the agent provides it with a trial run to ensure no mistakes exist in the coding.
Owing to these functionality, the process has been adopted across all corners of the manufacturing market, and CNC making is specially crucial in areas of material and plastic development. Discover more about the types of machining systems used and how CNC machine coding fully automates COMPUTER NUMERICAL CONTROL manufacturing below:
Open Closed-Loop Machining Systems
In the course of the CNC making process, position control is determined by using a open-loop or closed-loop system. With the former, the signaling runs in a single direction amongst the CNC controller and motor. With a closed-loop system, the controller is ready of acquiring responses, which makes problem correction possible. As a result, a closed-loop system can rectify unevenness in velocity and position.
In COMPUTER NUMERICAL CONTROL machining, movement is usually directed across X and Sumado a axes. The tool, in turn, is positioned and well guided via stepper or servo motors, which replicate exact activities as decided by the G-code. In case the drive and speed are minimal, the task can be run via open-loop control. To get everything else, closed-loop control is necessary in order that the speed, reliability and accuracy required for professional software, such as metalwork.
CNC Machining Can be Fully Computerized
Throughout today’s CNC methods, the production of parts via preprogrammed applications are mostly computerized. The dimensions for specific part are set into place with computer-aided design (CAD) software and then converted into an actual done product with computer-aided manufacturing (CAM) software.
Any given workpiece could necessitate a variety of machine tools, such as drills and blades. In order to accommodate these needs, many of modern day machines incorporate many different functions into one cell.
Alternately, an installation might are made up of several machines and a collection of automatic hands that shift parts from a single app to another, good results . everything manipulated by the same program. Regardless of the setup, the COMPUTER NUMERICAL CONTROL process provides for persistence in parts generation that would be difficult, or even impossible, to replicate physically.
The Different Sorts of CNC Machines
Typically the first numerical control machines date to the 1940s when motors were first employed to control the movement of pre-existing tools. While technologies advanced, the mechanisms were increased with analog personal computers, and finally with digital computers, leading to the climb of CNC engineering.
The vast the greater part of today’s COMPUTER NUMERICAL CONTROL arsenals are completely electronic. Some of the more usual CNC-operated processes include ultrasonic welding, hole-punching and laser cutting. Typically the most frequently used machines in COMPUTER NUMERICAL CONTROL systems include the following:
CNC Generators
CNC mills are capable of working on programs composed of number- and letter-based prompts that guide pieces across various distances. Typically the programming utilized for a mill machine could be according to either G-code or any unique language manufactured by a manufacturing team. Basic mills incorporate a three-axis system (X, Y and Z), though most newer mills can accommodate three additional axes.
Lathes
Inside lathe machines, bits are cut in a circular course with indexable tools. With CNC technology, the cuts applied by lathes are carried out with precision and high velocity. CNC lathes are widely-used to produce complex designs that wouldn’t be possible on manually run versions of the machine. Overall, the control functions of CNC-run mills and lathes are very similar. As with CNC mills, lathes can be instructed by G-code or unique proprietary signal. However, most COMPUTER NUMERICAL CONTROL lathes incorporate two axes -Back button and Z.
Flat screen Cutters
In the flat screen cutter, a flat screen torch cuts the material. The process is foremost applied to metal materials but can even be applied on other floors. In order to produce the acceleration and heat necessary to cut steel, plasma is developed through a combo of compressed-air petrol and electrical charmilles.
Electric Discharge Equipment
Electric-discharge machining (EDM) -alternately called to as expire sinking and of curiosity machining -is a process that molds workpieces into particular shapes with electrical sparks. Using EDM, current secretions occur between two electrodes, and this removes parts of a given workpiece.
If the space between the electrodes becomes smaller, the electric field becomes more powerful so tougher than the di-electric. This makes it easy for a current to pass between your two electrodes. Subsequently, portions of a workpiece are removed by each electrode. Subtypes of EDM include:
Wire EDM: Wire EDM makes use of spark erosion to remove portions from an electronically conductive material.
Sinker EDM: Sinker EDM employs an electrode and workpiece soaked in dielectric fluid when it comes to piece formation.
In the process known as flushing, debris from each finished workpiece is carried away with a liquid di-electric, which appears once the current between the two electrodes has stopped and it is meant to eliminate any more electric charges.
Water Jet Blades
In CNC engineering, water jets are tools that reduce hard materials, such as granite and metal, with high-pressure applying water. Within some cases, water is mixed with sand or some other strong harsh substance. Companies often condition factory machine parts through this process.
Water aircraft are employed as a cooler option for materials that cannot bear the heat-intensive processes of other CNC machines. Because of their cooler character, several sectors like the aerospace and mining industries depend on water aircraft, where they use them for making and cutting, among other functions. Businesses also use drinking water jet cutters for applications requiring very intricate cuts in material, as the insufficient heat helps prevent any change in the material’s inbuilt properties that could outcome from metal on metal cutting.
Exactly what Else Can a CNC Machine Perform
As plenty of CNC machine movie demonstrations have shown, companies use COMPUTER NUMERICAL CONTROL machines to make highly detailed slashes out of metallic pieces for business hardware products. Within addition to the aforementioned machines, you can find a number of other common pieces of machinery used in CNC manufacturing to produce highly comprehensive and accurate COMPUTER NUMERICAL CONTROL products. Some of the most regular products produced by CNC machines include steel aerospace components, metal automotive components, wooden decorations and plastic consumer goods pieces.
Since these CNC products have unique requirements, COMPUTER NUMERICAL CONTROL machines regularly utilize other tools and components. Check away some of the main pieces of equipment used within COMPUTER NUMERICAL CONTROL systems:
Embroidery machines
Wood routers
Turret punchers
Wire-bending machines
Foam cutters
Laser blades
Cylindrical mills
3D printers
Glass blades
Since COMPUTER NUMERICAL CONTROL machinery can apply so many other tools and components, you can trust it to create an almost limitless variety of goods quickly and accurately. With regard to example, when complicated cuts have to be made at various levels and angles on a workpiece, it can all happen within minutes on a CNC machine.
As long as the equipment is designed with the responsibility cod