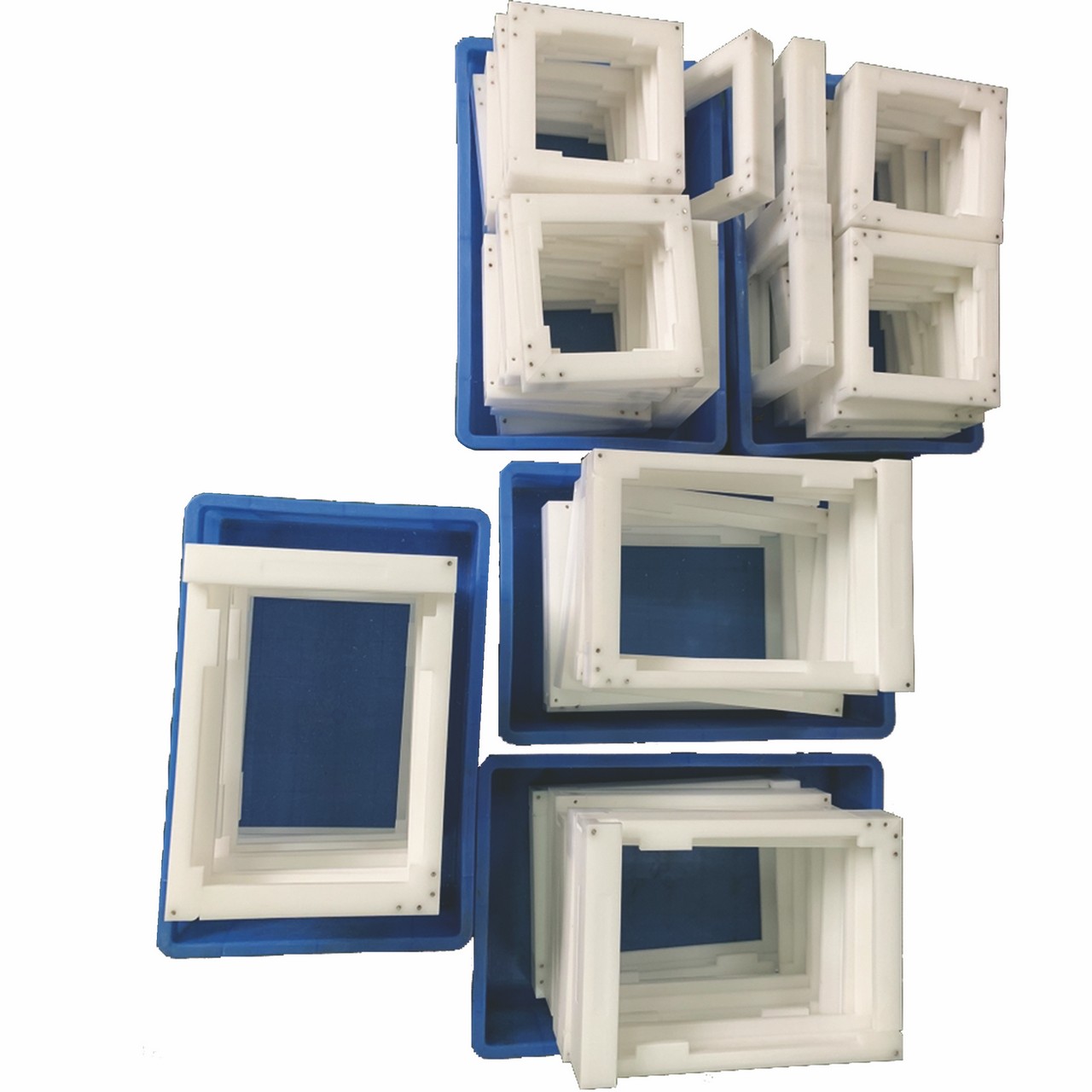
Injection molding machines perform a wide range of mechanical movements with differing characteristics. Mold opening is a low-force high-speed movement, and mold closing a high-force low-speed movement. Plasticizing involves high torque and low rotational speed, while injection requires high force and medium speed. A source of motive power is needed to drive these movements. The modern injection molding machine is virtually always a self-contained unit incorporating its own power source. Early machine frequency ran from a centralized source serving an entire shop or factory. In this respect, injection molding machines have undergone the same metamorphosis as machine tools.
Oil hydraulics has become firmly established as the drive system for the vast majority of injection molding machines and until recently was almost unchallenged as the power source. Put at its simplest, the injection molding machine contains a reservoir of hydraulic oil which is pumped by an electrically-driven pump at high pressure, typically at up to 2000 psi, to actuating cylinders and motors. High and low pressure linear movements are performed by hydraulic cylinders, and rotary movements for screw drive and other purposes are achieved by hydraulic motors. Hybrid machines, in which the screw is driven by electric motor while the linear movements remain hydraulically powered, are not uncommon.
In recent years, the supremacy of the hydraulic machine has been challenged by all-electric machines. These use new brushless servo motor technology to power the various machine movements. The capital cost of all-electric machines is higher than that of conventional machines but the energy consumption in production is much lower. This is because the electric motors run only on demand, and there are no losses due to energy conversion, pipelines, or throttling. The elimination of hydraulic oil makes the all-electric machine inherently cleaner, so these machines are attractive for sterile or clean room use. There is also evidence that all-electric machine movements can be resolved with a higher degree of precision and repeatability than hydraulic systems.
The process may involve either a thermoplast or a duroplast as the polymeric binder. With a thermoplast, solidification of the melt occurs on cooling; with a duroplast, a hardener is added to the feed mixture and solidification results from a binder-hardener reaction that occurs at elevated temperature. Figure 1 shows the viscosity-temperature relation for each type of binder. The reversibility of a thermoplast in terms of solidification makes recycling the reject a possibility but can lead to deformation of the compact during the subsequent burnout stage (see Sect. 3). For the duroplast process, solidification is irreversible and no deformation can occur during reheating, but the time for hardening is relatively long and the mold temperature is relatively high, and the reject cannot, of course, be recycled. The thermoplast process is the most widely used for ceramics and so this is discussed here.
Sign in to download full-size image
Figure 1. Fluidity of (a) a duroplast and (b) a thermoplast: Tfds(Tfts) and Tfde(Tfte) are the start and end temperatures, respectively, of fluidity of the duroplast (thermoplast);– –, range of reversibility
The principle of the operation of the injection molding machine is illustrated in Fig. 2. Granules are fed to the machine and then transported by a screw or a plunger to the heating chamber, from which the fluid hot mixture is injected into the mold. In the mold, the melt passes through a mean channel (sprue) to different side channels (runners) ending in cavities of the desired shapes. After filling the mold, the mass cools and solidifies; the mold is then opened and the products, runner and sprue are ejected. Nine major controls are available to the molding machine operation, and these govern:
LIM is a variation of the RIM process. The major difference is in the manner in which the liquid components are mixed. In the LIM process the entire shot is mixed in a chamber before injection into the mold, rather than being continuously mixed and injected, as in the RIM process. Accordingly, LIM is used to mold smaller parts, under 5 pounds (2.27 kg), which are below the capacity of RIM equipment currently available. LIM allows higher–viscosity materials, such as filled materials for shoe soles, to be used (5).
Abstract
Ceramic injection molding (CIM) is an integrated technology combined with powder technology, injection molding and sintering science. Mass production of ceramic parts with dimensionally accurate and complex shape can be realized by CIM. This paper presents the fundamental knowledge fully on CIM from the material selection to the final sintering process. It introduces properties of ceramic powder, binder system and the feedstock, and then mixing process of feedstock is demonstrated. The injection molding of feedstock is also analyzed. Especially for the key important process, debinding, has been indicated and discussed a lot. CIM is a complex processing technique. Different ceramic powder with different binder system needs suitable injection molding and debinding process which are all necessary to be investigated in order to ensure its efficiency and productivity. This paper shows you the critical issues to determine the appropriate process besides the basic theories on CIM.
(a)
the amount of material introduced into the cylinder,
(b)
the pressure applied to the plunger,
(c)
the plunger speed,
(d)
the temperature of the heating cylinder (and nozzle if controlled),
(e)
the temperature of the mold,
(f)
the plunger forward time,
(g)
the mold closed time,
(h)
the clamping force, and
(i)
the mold open time.
Other controls may be provided, depending on the design and intended use of the machine.
Figure 3 shows the mold pressure cycle during one stroke. The subdivision of the molding cycle into the steps of Fig. 3 is based on consideration of the pressure along the material axis in the mold. The dead time (a) is the time before the material starts flowing into the mold. In the next period (b) the material fills the cavity. As soon as the cavity is filled, the pressure increases rapidly and packing (c) occurs. At this stage, flow into the cavity is at a very slow rate. The compressibility of the material allows some flow during pressure buildup. Also, as the material cools in the mold it contracts, allowing more to enter. When the ram is returned, the gate is usually still relatively fluid in the case of a large gate and a thick part. Owing to pressure differences, reverse flow or discharge (d) occurs. Further cooling causes sealing (e) at the gate of the cavity, and no further flow in or out of the cavity is possible. With smaller gates, sealing occurs more rapidly, and common practice is to time the ram to return after sealing, thus preventing discharge. The remaining pressure in the cavity decays during the sealed cooling (f) until the mold is opened. Usually, there is pressure remaining in the cavity just before part ejection. Too high a residual mold pressure can cause sticking, scoring or cracking.
6.3.12 RRIM/SRIM summary
?
SRIM technology allows high fiber reinforcement content.
?
RRIM/SRIM is not limited to polyurethanes, other thermoset resins can be used. Examples that can be made from biological precursors are epoxies and polyamides.
?
The design of RIM machines does away with the need to solvent flush between shots (a drawback of RTM).
?
A precision engineered mixing head allows jets of the component materials to be fired into one another at high speed (Reynolds number of greater than 300). Coupled with precision control of dispense ratios, this high-quality mixing minimizes residual unreacted component materials in the finished moldings.
?
Residence time within the mixing head is of the order of 20 ms, therefore very fast reacting chemical systems can be used.
?
RRIM/SRIM has a high capital cost of plant (equivalent to thermal injection molders) and higher cost of tooling—higher than RTM, but not as high as thermal injection molding.
?
RRIM/SRIM machines minimize exposure of the workforce to unreacted chemical components.
Compared with the dry-pressing technique, injection molding can be used for making complicated forms owing to the high fluidity of the mass during the filling of the mold. In dry pressing, the “fluidity” of the granules disappears. Another advantage of the high fluidity of the injection-molding mixture is the homogeneity of the compact. In contrast with dry pressing, the morphology of the feed granules disappears completely. Relative to dry pressing, the cycle time is very long and the cost of the mold is very high. Also, the binder content of injected compacts is much higher than that of dry-pressed ones.