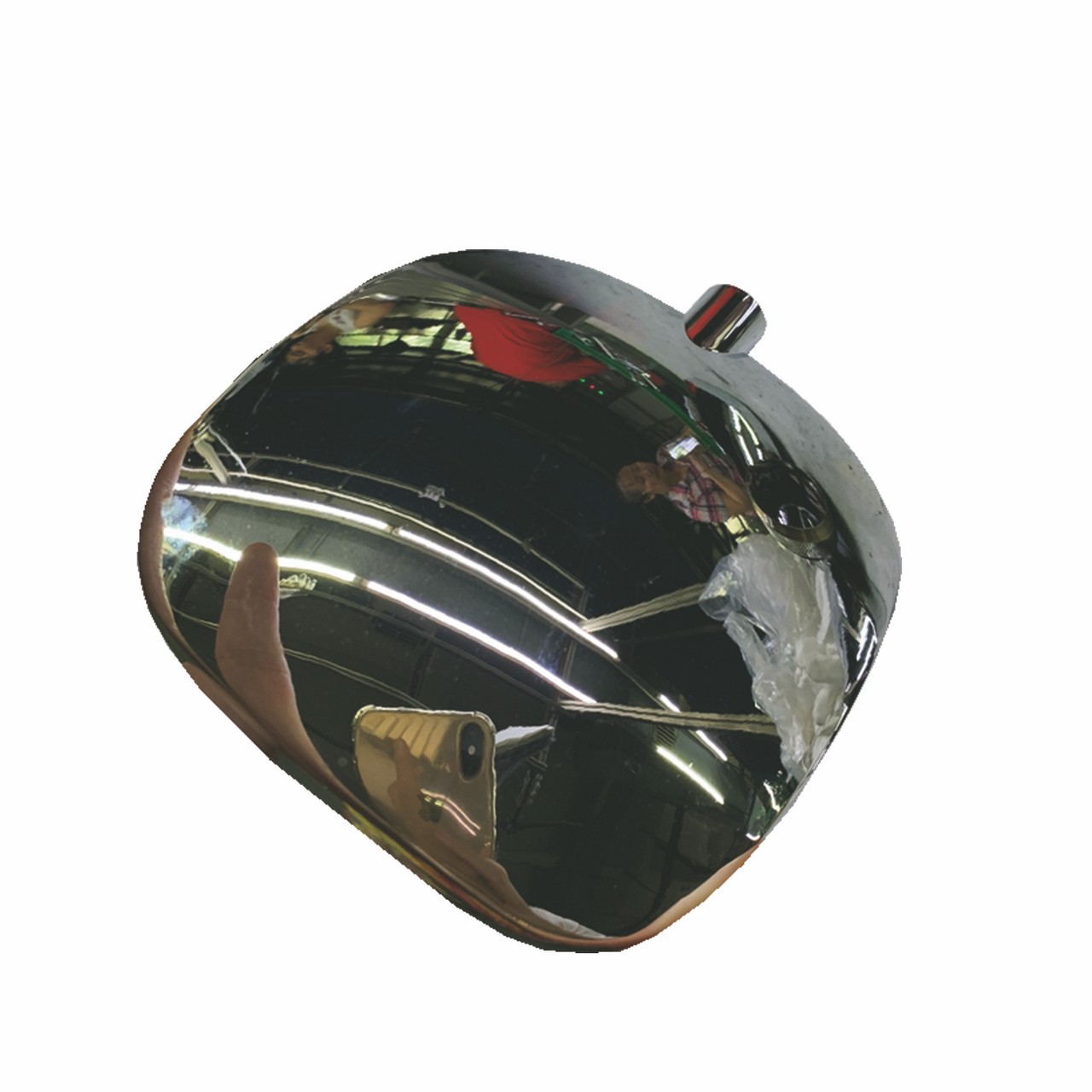
Injections molding is the most widely used developing process for the fabrication of plastic-type material parts. Lots of products are created using injection molding, which vary greatly in their size, intricacy, and application. Typically the injection molding process requires the use associated with an injection creating machine, raw plastic-type material material, and a mold. The plastic-type material is melted in the injection creating machine and then injected into the mold, where it cools and confirms into the ultimate part. The steps in this process are described in greater detail in the next segment.
Injection molding machine guide
Injection creating guide
Injection creating is employed to produce thin-walled plastic elements for lots of apps, one of the extremely recurrent being plastic enclosures. Plastic housing is a thin-walled box, often requiring many ribs and companies on the inside. These housings are widely-used in a variety of products including household appliances, electronic devices, power tools, as automotive dashboards. Various other common thin-walled products include different types of open pots, such as also. Injection molding is also used to produce several every day items such as toothbrushes or small plastic toys. A lot of medical devices, including valves and syringes, are created using injection molding as well.
Come back to top
Capabilities
Typical Feasible
Forms: Thin-walled: Cylindrical
Thin-walled: Cubic
Thin-walled: Intricate
Flat
Part size: Envelope: 0. 01 in3 - 70 ft3
Weight: zero. 5 oz - 55 lb .
Elements: Thermoplastics
Mêlé
Elastomer
Thermosets
Surface surface finish - Ra: 4 - 16 μin 1 - 32 μin
Tolerance: ± zero. 008 in. ± 0. 002 in.
Max wall fullness: 0. 03 - 0. 25 in. 0. 015 - 0. 5 in.
Quantity: 10000 - 1000000 1000 - a million
Lead time: Months Weeks
Advantages: Can build complex shapes and fine details
Exceptional surrface finish
Excellent dimensional accuracy
Substantial production rate
Minimal labor cost
Discarded can be used again
Disadvantages: Limited to thin walled elements
High tooling and equipment cost
Very long lead time possible
Applications: Housings, pots, caps, fittings
Assess with:
Get
Palinode: All process technical specs reflect the approx . range of a process's functions and may be viewed only as a guide. Actual functions are dependent after the manufacturer, equipment, stuff, and part requirements.
Return to top
Process Cycle
The method cycle for injections molding is very short, typically between 2 seconds and 2 minutes, and involves the next four stages:
Clamping - Prior to the injection of the material into the mold, the two halves of the mold must first be firmly closed by the clamping unit. Each and every half of the mold is affixed to the injections molding machine then one half is in order to slide. The hydraulically powered clamping product pushes the mould halves together and exerts sufficient power to keep the mold securely sealed even though the material is injected. The time required to shut and clamp the mold is centered following your machine - larger machines (those with greater clamping forces) will require more time. On this occasion can be predicted from the dried cycle time of the appliance.
Injection - The raw plastic-type material material, usually in the form of pellets, is provided into the injections molding machine, and advanced towards the mold by the injection unit. In the course of this process, the material is dissolved by heat and pressure. The smelted plastic is then injected into the mold right away and the buildup of pressure packs and holds the cloth. The amount of material that is injected is called the shot. The injections time is difficult to calculate effectively due to the complex and modifying flow of the molten plastic into the mold. Yet , the injection time can be predicted by the picture volume, injection pressure, and injection electrical power.
Cooling - Typically the molten plastic that is inside the mold commences to cool as soon as much more contact with the interior mold floors. As the plastic-type material cools, it will solidify into the condition of the specified part. However, during cooling some shrinking of the part may occur. Typically the packing of stuff in the injections stage allows additional material to stream into the mould and reduce the amount of clear shrinkage. The mould can not be opened before the required cooling the past. The cooling time can be predicted from several thermodynamic properties of the plastic and the ideal wall thickness of the part.
Disposition - After sufficient the passed, the cooled part may be ejected from the mold by the ejection system, which is affixed to the shoe half of the mold. If the mould is opened, a mechanism is employed to push the part from the mold. Power must be applied to eject the business because during cooling the part shrinks and sticks to to the mould. In order to facilitate the disposition of the part, a mold release agent can be sprayed onto the surfaces of the mold cavity previous to injection of the material. Typically the time that's needed is to wide open the mold and eject the business can be predicted from the dried cycle time of the appliance and should include moment for the part to slide free of the mold. Once the part is thrown, the mold can be clamped closed for the next shot to be injected.
After the injection molding pattern, some post control is typically required. During cooling, the fabric in the channels of the mold will harden placed on the part. This excess stuff, along with any flash that has occurred, must be trimmed from the part, typically by using cutters. For a lot of types of stuff, such as thermoplastics, the scrap stuff which will end result from this cutting off can be reused if it is located into a plastic mill, also called as regrind machines or granulators, which regrinds the discarded material into pellets. As a result of some wreckage of the stuff properties, the regrind must be merged with raw stuff in the proper regrind ratio to be reused in the injection creating process.
Injection cast part
Injection cast part
Return to top
Tools
Injections molding machines have many components and are available in several configurations, including a horizontal settings and a top to bottom configuration. However, irrespective of their design, all injection molding machines utilize a electrical power source, injection product, mold assembly, and clamping unit to perform the four stages of the process cycle.
Injections unit
The injections unit is in charge of both heating and treating the material into the mold. Typically the first part with this unit is the hopper, a sizable textbox into which the raw plastic is poured. The hopper has a open underside, that enables the stuff to feed into the barrel. Typically the barrel contains the mechanism for warming and injecting the material to the mould. This mechanism is usually a memory injector or a reciprocating screw. A new ram injector pushes the fabric frontward through a heated up section with a ram or plunger that is usually hydraulically powered. Right now, the more common strategy is the use of a reciprocating screw. A new reciprocating screw goes the material frontward by both spinning and sliding axially, being powered by either a hydraulic or electric electric motor. The fabric makes its way into the grooves of the screw from the hopper and is advanced for the mold as the screw rotates. Although it is superior, the material is melted by pressure, friction, and additional heaters that encircle the reciprocating mess. The molten plastic-type can now be injected very quickly to the form through the nozzle at the conclusion of the barrel or clip by the accumulation of pressure and the forward action of the mess. This increasing pressure allows the cloth to be jam-packed and forcibly preserved in the form. After the material has solidified inside the mold, the mess can retract and fill with more material for photo.
Injection molding machine injection device
Injections molding machine - Injection device
Clamping unit
Ahead of the injections of the smelted plastic to the form, the two halves of the form must first be securely closed by the clamping device. When the form is attached to the injection creating machine, each 50 percent is attached to a huge plate, known as platen. The particular front half the mold, called the mold cavity, is mounted to a stationary platen and aligns with the nozzle of the injection unit. The particular rear half the mold, called the mold core, is mounted to a movable platen, which slides along the tie bars. The particular hydraulically powered clamping motor actuates clamping bars that press the moveable platen towards the immobile platen and apply sufficient force to keep the form securely closed while the material is injected and eventually cools. Following the required cooling time, the mold can now be opened up by the clamping motor. An disposition system, which is attached to the trunk half of the mold, is actuated by the ejector bar and pushes the solidified part out of the open hole.
Injection molding machine clamping device
Injections molding machine - Clamping device
Device specifications
Injection creating machines are generally recognized by the dégaine of the grip force they provide. The necessary clamp push is dependent upon the forecasted part of the parts in the mold and stress with which the material is inserted. Therefore, a greater part will require a greater clamping force. Likewise, certain materials that need high injection challenges may require higher tonnage machines. The particular size of the business must also comply with other machine specifications, such as shot capacity, clamp stroke, lowest mold thickness, and platen size.
Injections molded parts may differ greatly in size and thus require these measures to cover a very large range. As a result, injection creating machines are made to each accommodate a little range of this greater spectrum of beliefs. Sample specifications are shown below for 3 different models (Babyplast, Powerline, and Maxima) of injections molding machine that are made by Cincinnati Milacron.
Babyplast Powerline Maxima
Clamp force (ton) 6. 6 330 4400
Shot capacity (oz. ) 0. thirteen - 0. 50 8 - 34 413 - 1054
Clamp cerebrovascular event (in. ) 4. 33 23. 6 133. 8
Minutes. mold thickness (in. ) 1. 18 7. 9 31. 5
Platen size (in. ) 2. 96 x 2. 95 40. 55 x forty five. 55 122. 0 back button 106. 3
Treatment molding machine
Treatment molding machine
Come back to top
Tooling
Typically the injection molding process uses molds, typically made of metallic or aluminum, as the custom pedaling. The mold has many components, but can be separated into two halves. Every single half is affixed inside the treatment molding machine and the rear 1 / 2 is allowed to slide in order that the mould can be exposed and closed alongside the mold's separating line. Both the main components of the mold are the mold core and the mold tooth cavity. If the mold is closed, the place between the mould core and the mold cavity varieties the part tooth cavity, that is filled with molten plastic to create the desired part. Multiple-cavity conforms are occasionally used, in which the two mold halves form several the same part cavities.
Treatment molding mold guide
Mold overview
Mould basic
The mould core and mould cavity are each mounted to the mold base, which can then be fixed to the platens inside the injection creating machine. The leading 1 / 2 of the mould base includes a support plate, to which the mould cavity is affixed, the sprue bushing, into which the material will stream from the nozzle, and a las vegas dui attorney ring, in order to align the mold base with the nozzle. Typically the trunk half of the mold basic includes the disposition system, to which the mold main is attached, and an assistance menu. When the clamping unit separates the mold halves, the ejector bar actuates the ejection system. The ejector tavern pushes the ejector plate forward inside the ejector field, which in convert pushes the ejector pins in the cast part. The ejector pins push the solidified part out and about of the wide open mold cavity.
Treatment molding mold basic
Mold base
Mould programs
In order for the smelted plastic to stream into the mould cavities, several programs are integrated into the mold design. First, the smelted plastic enters the mold through the sprue. Additional programs, called runners, hold the molten plastic-type material from the sprue to all of the cavities that must be loaded. At the ending of each and every runner, the molten plastic goes in the cavity through a gate which directs the stream. The molten plastic-type material that solidifies inside these runners is attached to the business and must be separated after the part has been ejected from the mold. Even so, sometimes hot jogger systems are widely-used which independently heat the channels, allowing the contained material to be melted and detached from the part. Another type of channel that is built in the mold is cooling down channels. These programs allow water to flow through the mold walls, next to the tooth cavity, and cool the molten plastic.
Treatment molding mold programs
Mold channels
Mould design
In addition to runners and gates, there a wide range of other design problems that must be considered in the design of the molds. Firstly, the mold must allow the molten plastic-type material to flow easily into each of the space. Equally important is the removal of the solidified part from the mould, so a pen angle must be applied to the mold walls. Typically the design of the mold must also accommodate any sophisticated features on the part, such as undercuts or posts, which will require additional mold bits. Most of these devices slide into the part tooth cavity through the area of the mould, and are therefore known as photo slides, or side-actions. Typically the most common type of side-action is a side-core which permits a undercut to be cast. Other devices enter into through the ending of the mould along the separating direction, such as internal core lifters, which can form an indoor undercut. To mold posts into the part, an unscrewing device is needed, which can rotate out and about of the mould after the posts have been produced.
Injection molding mould
Mold - Sealed
Injection molding mould exploded view
Mould - Exploded view
Come back to top
Elements
There are various types of materials that may be used in the injection creating process. Most polymers can also be used, including all thermoplastics, some thermosets, and a few elastomers. If these materials are widely-used in the treatment molding process, their raw form is usually small pellets or a fine powder. Also, tinctoriaux may be included in the process to regulate the color of a final part. The selection of a material for creating injection cast parts is not solely based after the desired characteristics of the ultimate part. While each material has different properties that will impact the durability and function of the final part, these properties also dictate the variables found in processing these materials. Each stuff takes a different fixed of processing variables in the treatment molding process, including the injection temperatures, injection pressure, mould temperature, ejection temperatures, and cycle time. A comparison of some commonly used materials is shown below (Follow the links to look for the fabric library).
Material name Abbreviation Trade names Description Applications
Acetal POM Celcon, Delrin, Hostaform, Lucel Strong, rigid, excellent fatigue resistance, excellent creep resistance, substance resistance, moisture weight, naturally opaque white, low/medium cost Bearings, cameras, gears, handles, plumbing related components, rollers, brake discs, slide guides, regulators
Acrylic PMMA Diakon, Oroglas, Lucite, Plexiglas Rigid, brittle, damage resistant, transparent, optic clarity, low/medium cost Display stands, knobs, improved lenses, light housings, energy, reflectors, signs, shelving, trays
Acrylonitrile Butadiene Styrene ABS Cycolac, Magnum, Novodur, Terluran Strong, flexible, low mold shrinkage (tight tolerances), chemical weight, electroplating capability, the natural way opaque, low/medium cost Automotive (consoles, panels, lean, vents), boxes, gauge, housings, inhalors, gadgets
Cellulose Acetate CA Dexel, Cellidor, Setilithe Tough, transparent, high cost Handles, eyeglass support frames
Polyamide 6 (Nylon) PA6 Akulon, Ultramid, Grilon High durability, fatigue resistance, substance resistance, low slide, low friction, almost opaque/white, medium/high cost Bearings, bushings, gears, rollers, wheels
Polyamide 6/6 (Nylon) PA6/6 Kopa, Zytel, Radilon High strength, fatigue weight, chemical resistance, low creep, low scrubbing, almost opaque/white, medium/high cost Handles, levers, small housings, zip jewelry
Polyamide 11+12 (Nylon) PA11+12 Rilsan, Grilamid High strength, tiredness resistance, chemical weight, low creep, low friction, almost maussade to clear, extremely high cost Air filters, spectacle frames, safety goggles
Polycarbonate PC Calibre, Lexan, Makrolon Very tough, temperature weight, dimensional stability, translucent, high cost Automotive (panels, lenses, consoles), wine bottles, containers, housings, light covers, reflectors, basic safety helmets and glasses
Polyester - Thermoplastic PBT, PET Celanex, Crastin, Lupox, Rynite, Valox Rigid, high temperature resistance, chemical weight, medium/high cost Automotive (filters, handles, pumps), bearings, cams, electrical components (connectors, sensors), armor and weapon upgrades, housings, rollers, fuses, regulators
Polyether Sulphone PES Victrex, Udel Tough, very high chemical resistance, clear, very high cost Valves
Polyetheretherketone PEEKEEK Strong, cold weather stability, chemical weight, abrasion resistance, low moisture absorption Aircraft components, electrical connectors, push impellers, seals
Polyetherimide PEI Ultem Heat resistance, flame weight, transparent (amber color) Electrical components (connectors, panels, switches), covers, sheilds, surgical tools
Polyethylene - Low Density LDPE Alkathene, Escorene, Novex Lightweight, challenging and flexible, excellent chemical resistance, natural waxy appearance, low cost Kitchenware, housings, protects, and containers
Polyethylene - High Density HDPE Eraclene, Hostalen, Stamylan Tough and stiff, excellent substance resistance, natural waxy appearance, low cost Chair seats, housings, protects, and containers
Polyphenylene Oxide PPO Noryl, Thermocomp, Vamporan Tough, heat resistance, fire resistance, dimensional steadiness, low water consumption, electroplating capability, high cost Automotive (housings, panels), electric parts, housings, plumbing related components
Polyphenylene Sulphide PPS Ryton, Fortron Very high durability, heat resistance, darkish, very high cost Bearings, covers, fuel products, guides, switches, and shields
Polypropylene PP Novolen, Appryl, Escorene Lightweight, heat weight, high chemical weight, scratch resistance, natural waxy appearance, challenging and stiff, low cost. Automotive (bumpers, covers, trim), wine bottles, caps, crates, manages, housings
Polystyrene - General purpose GPPS Lacqrene, Styron, Solarene Brittle, transparent, low cost Cosmetics packaging, writing instruments
Polystyrene - Substantial impact HIPS Polystyrol, Kostil, Polystar Impact strength, rigidity, sturdiness, dimensional stability, the natural way translucent, low cost Electronic housings, food storage units, toys
Polyvinyl Chloride - Plasticised PVC Welvic, Varlan Tough, flexible, flame weight, transparent or maussade, low cost Electrical efficiency, housewares, medical lines, shoe soles, gadgets
Polyvinyl Chloride - Rigid UPVC Polycol, Trosiplast Tough, adaptable, flame resistance, translucent or opaque, low cost Outdoor applications (drains, fittings, gutters)
Styrene Acrylonitrile SAN Luran, Arpylene, Starex Stiff, brittle, chemical weight, heat resistance, hydrolytically stable, transparent, low cost Housewares, knobs, syringes
Thermoplastic Elastomer/Rubber TPE/R Hytrel, Santoprene, Sarlink Tough, flexible, high cost Bushings, electric parts, finalizes, washers
Go back to top
Cost Motorists
Material cost
The particular fabric cost is determined by the of material that is required and the unit price of that materials. The weight of fabric is obviously a direct result the part volume and materials density; nevertheless , the part's maximum walls thickness can also play a role. The of materials that is required includes the materials that fills the channels of the mold. The dimensions of those channels, and therefore the amount of materials, is essentially decided by the width of the part.
Production cost
The particular production value is mainly calculated from the hourly rate and the cycle time. The hourly rate is proportional to the size of the injection creating machine being used, so it is important to understand how the part design impacts machine selection. Injection creating machines are typically known by the tonnage of the clamping force they provide. The necessary clamping force is dependent upon the projected part of the part and stress with which the material is injected. Therefore, a bigger part will require a bigger clamping pressure, and therefore a more expensive machine. Furthermore, certain materials that require high shot pressures may require higher tonnage machines. The dimensions of the part must also adhere to other machine specs, such as grip stroke, platen size, and shot capacity.
The cycle time can be separated into the shot time, cooling time, and resetting time. By reducing any of these times, the production cost will be reduced. The injection time can be reduced by reducing the maximum wall width of the business and the part volume. The chilling time is also decreased for lower wall thicknesses, as they need less time to cool all the way through. Several thermodynamic properties of the material also affect the cooling time. Finally, the resetting time depends upon the machine size and the part size. A bigger part will require larger motions from the equipment to open up, close, and remove the part, and a larger machine requires more time to perform these operations.
Tooling cost
The tooling cost has two main components - the mold base and the machining of the cavities. The price of the mold foundation is mainly managed by the size of the part's envelope. A bigger part requires a bigger, more expensive, mildew base. The cost of machining the cavities is impacted by almost every factor of the part's geometry. The particular primary cost car owner is the size of the hole that must be machined, measured by the projected area of the hole (equal to the projected area of the part and projected holes) and its depth. Some other elements that will need additional machining time will add to the cost, including the feature count number, parting surface, side-cores, lifters, unscrewing devices, tolerance, and surface roughness.
The amount of parts also impacts the pedaling cost. A bigger manufacturing quantity will need a higher class mildew that will not wear when. The particular more powerful mold materials results in a greater mold base cost and more engineering time.