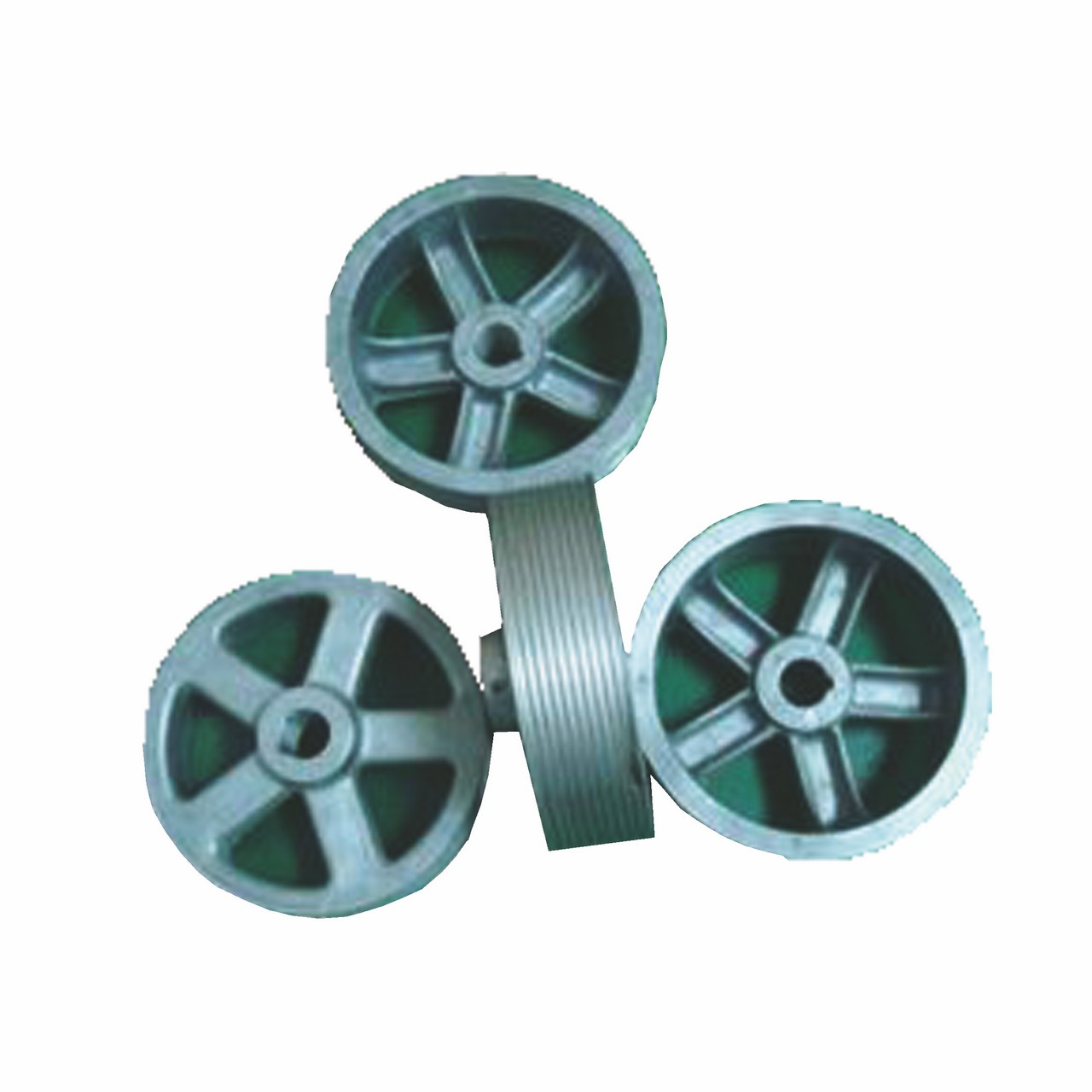
What is Investment casting?
On Investment casting, a wax or simply suitable polymer pattern is included in dipping to the refractory material slurry. Once the refractory materials coating is hardened then this sort of dipping process is repeated several times to raise the covering thickness and its particular strength. When the last coating is solidified the wax is melted away and molten metal is put in to the cavity created by simply the wax pattern. When the material solidifies inside the mould, material casting is removed by damaging the refractory mould.
Schematic illustration from Investment casting
Figure 1. Schematic illustration of Investment casting
While demonstrated in figure 1, the duty could be summarised in these steps– Master style making, Master die manufacture, Style making, Pattern assembly, refractory mildew making, dewaxing, casting, and portion removal.
Investment casting known while lost wax casting is some precision metal casting process whilst it is with the capacity of having high accuracy and intricately thorough castings when comparing to similar manufacturing operations such as for instance sand casting.
Adverts
Advertising
Typical parts include generator rotors, gears, electronics enclosures, regulators, jewellery and dental fixtures. Parts around 1. 5 l in diameter and weighing around 1140 kg have really been cast successfully in the previous by this method, even even so the typical part can have typically not nearly as expensive 100 milimetre in proportions and weighs reduced than 500 g.
Gas turbine brake rotor investment casting( Source: Howmet Corporation)
Figure 2 Gas turbine brake rotor investment casting( Source: Howmet Corporation)
Figure 2 shows a gas turbine rotor casting at several stages.( Wax pattern, ceramic layer coating across the wax style, molten metal fill stage& final investment casting)
Backgroundfrom Investment sending your line
Although Investment sending your line have been found in several sorts because it was utilized by ancient Egyptians between 4000 and 3000 B. C, it is just after World War 2 its commercial importance and acceptance grew because of the getting regarding parts in issues the plane engines and airframe sector.
Shed wax casting has evolved from the days where clay was initially packed round the bee 's polish pattern to the utilization of ceramics covers and the creation of particular dewaxing ovens etc.
The best manufacturing price of master becomes deceased has traditionally limited investment throwing to large production quantities, yet the development of additive production or 3D printing of polish patterns lately offers eliminated the manufacturing cost in dies and enabled the take advantage of for shorter runs.
Advertising
Advertisement
Pros and cons investment throwing
Features of Investment casting
Elementswith extremely complex shapes and intricate features may be solid like an individual piece using expense throwing
With short length or simply shallow depth feature, thin areas as a result of 0. 40 mm( 0. 015 in) may be solid without cold shut defects
Shed wax casting has excellent dimensional accuracy and tighter tolerances in 0. 075 mm( 0. 003 in) in many cases are achievable.
When compared with similar manufacturing processes, Investment audition can perform a great exterior finish without any post a significant processing. Typically around 1. 3 or maybe more– 0. 4 microns RMS Ra
It includes almost infinite freedom in terms of investment cast elements, but the most often found materials employed include Aluminium alloy, cast with regards to iron and non- ferrous other metals. The procedure is specially desirable for high- temperature metals.
Draft on walls are by no means required in case a grasp die is utilized to create wax patterns then draft hard would ensure that the pattern production process easier.
And there is no parting lines, the cast might not have any sort of flash. Nevertheless the wax signs could have parting lines inside the master die.
Additional machining could be eliminated or reduced and an excellent allowance of only a small amount because 0. 4 to at least one millimeter( 0. 015 to 0. 040 in.) is usually enough.
Superb dimensional precision could be performed on mixture with very smooth because- cast surfaces. These capabilities are specially attractive when designing items from positive aspects- burning temperature, difficult- to-- machine metals that may not become cast with plaster- or simply metal mould processes.
The polish used usually can be retrieved for reuse.
Down sidesof Expense casting
In comparison with other methods from metal casting including Die audition and sand casting, lost wax tart casting involves many complex measures making the method relatively high- priced. But a number of the measures may be automated for many merchandise. It may be more pricey in opposition to the way die casting or sand audition, but per- unit costs decrease with large volumes.
The very high cost dies to create patterns has traditionally an issue investment casting to large formation quantities
The high price can even be as a result of specialised tools requirements, costly refractory material, and high labour cost
Parts are already challenging to cast if lots of people require cores, got holes small than 1. 6 mm in addition to deeper than 1. 5 moments the diameter
Ad
Ads
The easiest way does Investment casting work?
So what the deuce will be the Investment casting practice steps?
Investment casting has truly been creating near- net kind products successfully in a variety of sorts for hundreds of years . Though the creation of new elements and manufacturing linked to the previous few years has xmas trees for some changes and changes, the investment casting process measures have largely remained unchanged.
For general, investment casting sometimes called to as lost wax audition could be summarised in to the pursuing 8 steps.
1– Master pattern creating
A specialist pattern is produced from wax tart, clay, wood, steel or plastic- type material by the specialised form maker or sculpture artist just like final product requirement. These are already made considering both wax and casting material shrinkage, hence it 's called, "master pattern" for achieveing double shrinkage allowance. Figure 3 or maybe more below shows a wooden get good at pattern as well as casting.
Expenseaudition Master style
Figure 3 Get good at pattern( source: garenphillips. com)
With respect to the size, form and materials, this method may take some trial and fault to find the size and form correct, therefore making every one of these moulds expensive.
step two– Master die/ Mould/ Mold
A mould, known whilst the master die to make wax tart patterns is built to in form the master pattern by sometimes casting or machining. Technology growth in tooling and CNC engineering has enabled machining a grasp die from your material this type of as steel and aluminium lacking the advantages of a specialist pattern as demonstrated fit 4.
graspdie
Figure 5. Master die
When the get good at pattern is created in steel then your master perish may be cast directly with the steel master pattern working together with metal with less shedding point than steel. Silicone plastic moulds double extensively these a short time because of the simplicity in serves to cast a mildew from a master routine. Silicone rubber moulds would tolerate casting temperature as much as regarding 310oC( 590oF).
expensecasting kick the bucket and cluster
Figure 5. Purchase casting die and cluster
The master pattern and master perish should be designed taking shrinking of pattern wax, refractory subject material as well as the metal cast materials under consideration. It is also great practice to add machining allowances to obtain post- machining on tight tolerance surfaces. Essential factor of two- part grasp dies or moulds is mildew alignment locators. Mould locators will soon be critical in aligning your two halves to create accurate parts without large parting lines or simply parting line shifts.( Figure 5)
3– Pattern
The patterns are then made by just injecting or pouring molten polish in to the master die and and can harden( Figure 6). The idea is also utilized like a coating where inside cavity walls from your die are in reality coated with wax to acquire a hollow pattern. This covering is repeated until preferred pattern thickness is reached generally about 3 mm( 0. doze in). Latter suitable only meant for simple parts. Sometimes patterns will even be made using suitable polymers and frozen mercury.
Figure six. Pattern making
Recent advances present in rapid prototyping associated with creation of patterns completely from a great CAD file possible, either such as a master pattern or as polish patterns, consequently reducing the purchase price. 3D printing technologies such because stereolithography, selective laser sintering( SLS), fused deposition modelling( FDM) and poly jetting are increasingly useful to create patterns. These quick prototyping technologies make use of a layering technique within their creation therefore post- processing is necessary generally to ensure a fantastic surface finish.
Cores will soon be generally created from soluble wax or simply ceramic where soluble wax callosité are dissolved out from the patterns pre- processing, as the ceramic cores remain and they're removed after solidification of the metal casting.
In an alternative called "Chasing" imperfections such because parting lines and flashings will undoubtedly be removed employing a heated steel tool and release agents, this sort of as silicone sprays are likewise used to aid in pattern removing and steer clear of any harm to the patterns.
Ad
Advertising
Period4– Pattern assembly
The wax patterns are then assembled onto a typical wax sprue. Sprue is really a channel throughout which molten alloy can reach the mould inside an investing band following the wax is still removed.
investment decisioncasting cluster
Figure six. Investment casting cluster
Using heated up tools and melted wax, your amount of wax patterns may easily be attached to a principal sprue and runner system to have a pattern cluster or if your tree. With regards to the specifications in the parts, about many hundred patterns could be constructed onto a tree increasing output.( Figure 7)
Sprue will hold the wax pattern to stay away from distortion throughout the casting plan of action , making a channel for that molten wax to flee from your mould after which enabling the molten material to stream in to the mould.
Stagefive– Dipping coating
The structure can then be dipped into the slurry of finely ground refractory material and from then on drained to have a uniform surface coating called a "Prime coat". Throughout that stage the finest compound dimensions are deposited to create a skinny but very smooth layer in investment material, to make certain an excellent easy surface and intricate thorough final product. Very fine silica and differing binders, including water, ethyl silicate, and acids are commonly used as refractory materials.
Physique 8. Investment_casting_refractory coating
After the original layer has dried, the pattern is dipped and layered repeatedly to boost its density for better strength. This second stage from the dipping method is known as "stuccoing" in which sand or other refractory become worse is rained within the moist surface to raise the density( 5 to fifteen mm]zero. 2 to 0. 6 within.]) and strength.
Often as a substitute method, the one- dipped pattern group is inserted inside a permeable flask inverted and liquid purchase material poured around it. The flask can now be vibrated to get rid of entrapped air create convinced the investment material encompases all surfaces inside the mould shrub.
This can now be left to be dried completely, that may have between 16 to 48 a long time. Drying may be accelerated simply by applying vacuum pressure or reducing environmental humidity.
Step six– De- waxing and taking photos
After the refractory material mildew has fully dried and treated, they could be turned inverted and found in the oven or possibly special purpose de- putting wax on autoclave, where in actuality the wax can easily melt and go out( figure 9), and any subsequent deposit vaporized.( These simulations show the easiest way specialised de- waxing models work video 1 or video tutorial 2)
Physique9 Investment audition dewaxing
Removing style wax from your mould can be an important stage inside the investment casting process and as soon as performed incorrectly wil dramatically reduce the batch yield. De- shaving can also be one of many causes of shell cracking. Layer cracking is an individual most wide- spread investing casting defect.
Fundamentally now you can find two main method of via- waxing, flash fire in addition to autoclave( steam). Steam autoclaves are actually the favored choice because of their uniform heating that could reduce the strain on the material.
The mould is started( 90oC–175oC) and in a great inverted position for a number of hours( about 4– doze hours) to allow wax to melt and come to an end. Style wax is usually recovered and recycled. It 's heated and maintained at an increased temperatures( 650oC–1095oC) for some time( 3- 6 hours), to push off the from crystallization and lose any kind of residual wax. The itemsduration along with temperatures depend on the fabric cast material.
Sobre- shaving séchoir
Figure 10. De a significant waxing autoclave
Most shell setbacks occur through the dewaxing point since the waxes used include a larger thermal expansion ratio compared to the refractory material. That is why wax expands more than investment material and introduces some possible stress fracture around the mould. To cut back this impact the wax could be warmed rapidly so the exterior polish melts quicker and allow the residual wax to expand without having stressing the mould. Autoclaves exhibited in figure 10 double to heat reduce this effect since the heating cycles can become more uniform and managed even better.
Stageseven– Preheat& Casting
Physique11 Casting stage
Mould can now be pre-- heated in preparation for flowing. Preheating allows the metal in which to stay the molten condition longer to ensure this can better fill all mold details and increase dimensional precision. In the event the mould is remaining to cool, any cracks discovered could be repaired with porcelain slurry or special cement. Mold heating also gives better dimensional control considering that the mould plus the metal can shrink together during cooling.
Molten metal as much as 3000oC is poured in the hollow mould and next left to cool. As the law of gravity pouring is the easiest, strategies might be used to make sure complete replenishing from the mould. When complicated, thin sections are participating, mold filling could be assisted by simply positive air pressure, tilt throwing, vacuum casting or centrifugal spreading process.
Stage8– Knockout& post- processing
Number 12. Put out of action casting removals stage
Following your metal features solidified, techniques such as for instance physical chipping, hammering, vibrating, high supports pressure water jetting and media blasting can be used to the mould and take away the steel casting.
Then individual castings are actually cut away and excess steel is removed. The sprue is certainly take off and in most cases reused. The business enterprise is certainly then post- processed found relative to the ultimate merchandise requirement such as for example post supports machining, heat treating, surface treatment plans, painting etc.
Expensecasting and 3D printing
The investment sending your line method advantages of additive developing in a number of techniques. Probably the most apparent advantage is we can get rid of moulds, and the strategy can simply immediately print patterns with exceptional details.
MoviePlayer
00: 00
00: 04
Imagecredit– google images
When combined, 3 DIMENSIONAL printing, the most recent manufacturing strategy and investment casting, the absolute most well- known metal forming technique, can lower development some tooling expense during engineering website.
Bypassing the most frequent approach of manufacturing a master pattern, mould and wax patterns, the 8 stage investment casting process could turn out to be reduced to fewer steps. Consequently considerably reducing production time by weeks to days.
Advantages of 3d printing investment casting behaviour
Reduce tooling costs because they build modest volumes of casted parts from your CAD model 24- 48 hours.
Reduce steadily the time it requires to create tooling.
Reduce the total amount from investment property and the sum space needed for application storage.
Supplynon- moldable goods