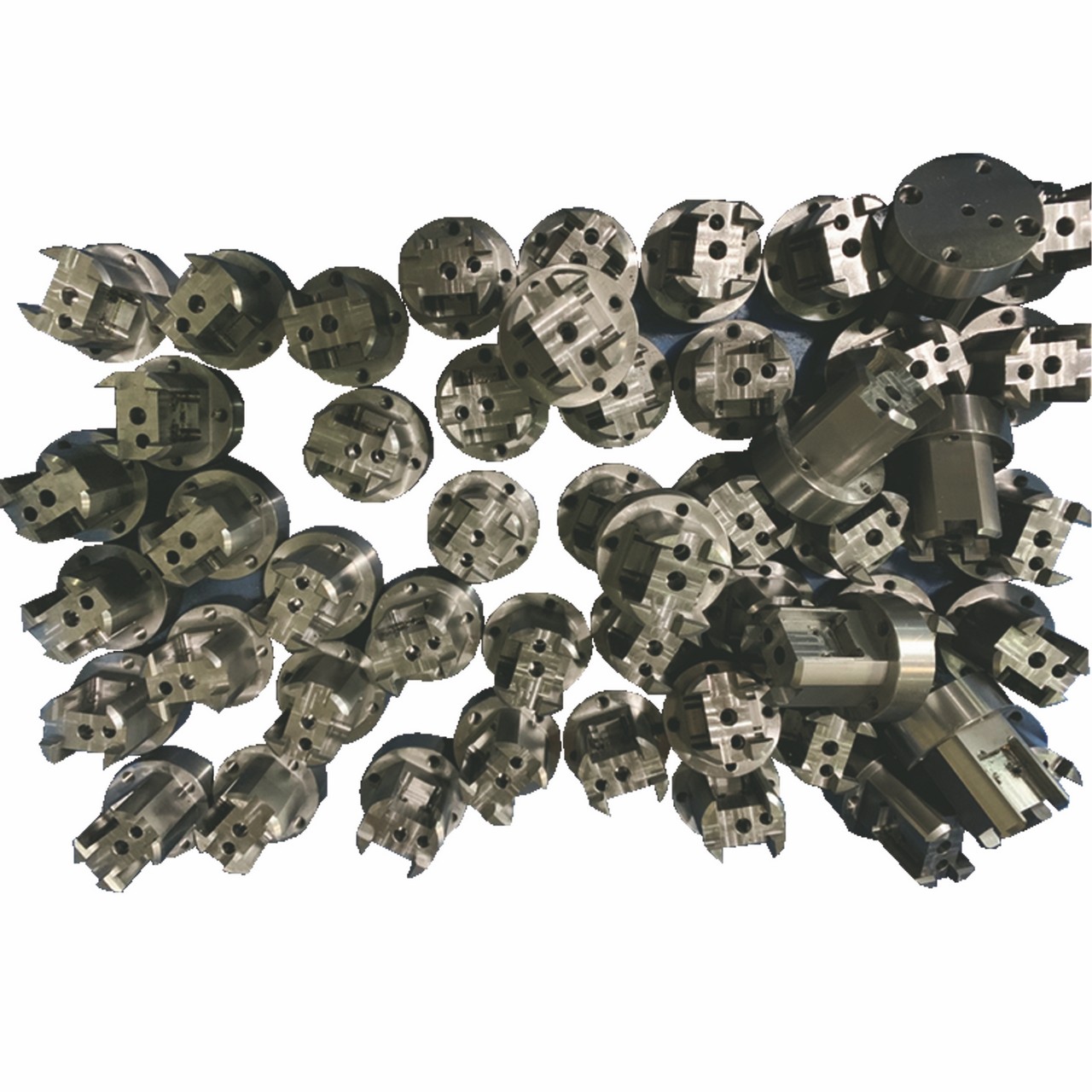
COMPUTER NUMERICAL CONTROL milling is one of processes when looking to generate intricate parts. Why intricate? Whenever other architecture methods like lazer or plasma reducing can receive the same results, it is cheaper to go with them. Although these two do not provide everything similar to the features of COMPUTER NUMERICAL CONTROL milling.
So, we intend to take a serious dive into milling, taking a look at the various aspects of the procedure itself as well as the equipment. It will help you understand if you need COMPUTER NUMERICAL CONTROL milling services to produce your components or is there a cheaper option available.
Table of Contents conceal
We What is COMPUTER NUMERICAL CONTROL Milling?
II Milling Process
III Milling Machine Components
4 Types of Milling Devices
V Exactly how Many Axes?
MIRE CNC Milling Businesses
VII Suitable Elements
What is COMPUTER NUMERICAL CONTROL Milling?
We are going to go through the process, machinery, and so forth in later paragraphs. Although let’s first make clear what COMPUTER NUMERICAL CONTROL milling means and bring clarity to a few of the more confusing points about the phrase itself.
Initial, people often ask for CNC engineering when looking for milling. Machining includes both milling and turning but these two have distinctive differences. Machining pertains to a physical cutting technology that uses physical contact to remove stuff, using tools.
Second, all CNC engineering uses CNC machines although not all COMPUTER NUMERICAL CONTROL machines are for machining. Computer statistical control is what lies behind these three letters. Virtually any machine using COMPUTER NUMERICAL CONTROL utilises computerised systems for automating the cutting process.
For that reason, CNC machines also include laser blades, plasma cutters, press brakes, etc.
And so CNC machining is a mix of these two words, bringing us the response to the question posed in the heading. CNC milling is a substractive fabrication method that uses computer statistical controls systems for automating the process.
Milling Method
Made part in steel chips
We're able to limit themselves to describing the fabrication process only but giving an overview of the whole flow gives a more wholesome picture.
The milling process includes:
Designing the parts in CAD
Translating the CAD files into signal for machining
Placing up the machines
Producing the elements
Designing the CAD files & interpretation into signal
Typically the first step is resulting in the virtual representation of the final product in CAD software. There are various powerful CAD-CAM programs that let the user create the necessary H code for engineering.
The code can be obtained for checking and amending, if necessary, to fit the machine’s capabilities. Also, production engineers can replicate the entire cutting process by using this kind of software.
This enables looking at for mistakes in the design to avoid creating models that are not possible to create.
Gary the gadget guy code written by hand, as was done in the previous. This, however, stretches the entire process substantially. Consequently, we would suggest making full use of the possibilities modern architectural software offers.
Environment up the appliance
Despite the fact that CNC machines do the cutting work automatically, many other areas of the process machine operator’s palm. For example, mending the workpiece to the worktable as well as fixing the milling tools to the spindle of the machine.
Manual milling will depend on heavily on the operators while modern models have more advanced automation systems. Modern milling zones may also have live tooling choices. This means they can alter the tools on the go through the manufacturing process. So there are fewer stops but someone still has to set them up beforehand.
Following your initial setup is carried out, the operator investigations the machine program one last time before giving the machinery a environmentally friendly light to get started on.
Find your metal architecture quote in just a few seconds
icon
Quote in seconds
icon
Brief lead times
symbol
Delivery by Fractory
Get quote
Manufacturing work
The milling process uses a rotating tool that makes contact with the workpiece to cut off potato chips. The continuous trimming results in the desired shape.
Presently there are, however, a few different ways to do the trimming:
Conventional milling
Ascend milling
Conventional milling process
As the name says, standard milling is the more common way to mill, at least in the past. The technicians of conventional milling:
The cutting nick increases in width. This could cause raised temperatures that produce work hardening.
The particular beginning of a cut includes more rubbing and rubbing, quickening the tool wear and reducing its lifespan.
Since the teeth carry potato chips upwards, they may fall back into the cutting route, decreasing the standard of the finish.
Tighter clamping and fixing of the workpiece is essential to avoid shift caused by the top upwards forces.
Ascend milling process
More recent CNC mills alternatively use climb milling. The features of climb milling are:
The cutting processor chip decreases in size, heating of the chip as compared with to the workpiece.
The cutting surface is cleaner, ending in less chaffing and an increase in tool life expectancy.
The chips autumn behind the used vinyl cutter, reducing of a polluted cutting journey.
Horizontal climb milling creates downward allows, reducing the need for extra clamping.
The milling process usually a few different functions but this the of the final product and the status of the fresh piece. Often, milling is necessary for providing a precise finish off and adding a few features like slots or threaded holes.
But it is also creating a finished part from a prohibit of fabric. Typically the first functions use larger tools to quickly carve away the material to fasten the task until getting to around of the last piece.
A tool change is essential to create the highly accurate machined components. The great accuracy milling is known for is achieved in the final stage, taking executive tolerances and surface roughness to levels difficult to match with any other manufacture process.
Milling Device Components
Now, let us see what makes up a milling machine. While new milling centres have the features to perform operations, also, they are more complicated. Thus we are adhering to the more traditional benches here to provide an review of the device components.
Horizontal milling machine
Horizontal milling machine components
Image source: technologystudent. possuindo
Horizontally milling machines get their be made from the location of the tool – their axis lies horizontally. Typically the images above show one way of with them which is plain milling. Of course, lateral mills are also milling.
The build of a lateral mill is rather simple. The chopping tool attaches upon the arbor. As soon as a change of tooling is necessary, you can remove the arbor clump and the coil spring spacers to replace tools.
Fixing the workpiece onto the working table requires a vise. The navigate can move the table in A, Y and Unces axis for moving the workpiece.
Involving course, newer machines look a little different, making them automation. Horizontal milling centres several spindles with a range of tools on them for quicker turnaround times. Also, the stand as well for the reason that tools can relocate more directions, including rotational axes.
Continue to, the basics are the same and understanding the more traditional machine is enough to sound right of the ones.
The horizontal milling:
Possibility to produce parts with less operations
Capability to create more complex elements
About 3-4x faster than vertical milling
Longer tool life
Better surface end (last 2 details are related to fewer chips dropping onto the slicing path)
Vertical milling machine
Vertical milling machine components
Graphic source: technologystudent. apresentando
Again, the name of a usable mill is incredibly self-evident when looking at the above. Like the positioning of the tool axis is vertical, it is better best suited for milling.
At this time there are a few distinctions between lateral and vertical milling machines. But components are still similar. The machine brain is a the of a ram. Typically the spindle for chopping tools is fastened to the brain.
Everything about the positioning of the table is the same to a lateral mill, providing the ability to move it in the same 3 guidelines.
The modern 5-axis vertical mills offer possibilities to move the business for more access and faster turnaround times. Automating all the movements results in better accuracy, more rapidly lead times and identical batches of parts.
The usable milling:
Considerably more affordable than horizontal generators, with an amount big difference up to 4-5x
Availability because more workshops are able them
Easier to use because the usable mill provides better visibility to what is actually occurring
More machinists who great results
Typically the machines are smaller, requiring less place in the COMPUTER NUMERICAL CONTROL machine shop
Different types of Milling Machines
There is also a lot of variety available on the market today. A lot of ways of category also exist. Typically the basics remain rather much the same everywhere, with a few modifications providing about more alternatives and hence another type of milling machine.
Here are types of milling machines:
Bed-type
Knee-type
Ram-type
Planer-type
Bed-type generators
bed-type milling machine
The design of bed-type milling machines includes a stable machine cargo area. While large and heavy parts can instability with knee-type machines, bed-type ones can take their soil. The long cargo area means that multiple parts can be attached onto the bed simultaneously, decreasing idle times and increasing the efficiency on the workfloor.
The worktable hooks up directly to your bed of the machine and can move in 2 directions. The spindle head, of course, can move axially to look for the cut interesting depth. The positioning of the axis the machine, as there are both lateral and vertical cargo area mills, as well as universal machines. All of them automated by using CNC.
The most frequent of these options is a COMPUTER NUMERICAL CONTROL universal milling machine. While horizontal and vertical mills come with considerable constraints, these machines provide more flexibility.
One other way to increase productivity is by using a two-machine stand. This specific helps to either mount many of parts onto the table for sychronizeds processing or one large part. This specific loses the requirement for re-clamping it to process one other ending. It is important to be aware that this setup opens the probability to tool collision which is often averted by a appropriate CNC program.
Knee-type milling machines
knee-type milling machine
These kinds of machines are suited to producing parts starting from small to medium size. The constraint arises from the reality that knee-type generators provide less stableness than, for example, bed-type milling machines. Also, the shape sets its own limits for part dimensions.
A regular knee-type mill is a superb option for producing one-off parts, maintenance work, preparatory tasks, and so forth Typically the unidirectional movement of the cutting brain limits the probability of accidents. Applying them for setting up the workpiece at a later time refining on a CNC station is common.
These machines require a handbook change of tools after every functioning, the whole process a bit slower. Nonetheless, modern CNC engineering centres include the features of knee-type milling machines.
Ram-type milling machines
Typically the ram-type mill has its cutting brain mounted on a ram that can slide back-and-forth. This specific increases the tool movement to 2 axes – Back button and Y. Equally horizontal and top to bottom selection of the memory mill are available on industry. A lot of of such generators also include the ability for swivelling the cutting brain.
Planer-type generator
Planer-type mills are incredibly similar to bed-type milling machines. Both have large worktables and spindles that can transfer 3 guidelines. The comes from the planer-type milling machines’ ability to accommodate more milling tools at once. The quantity of different tools usually goes upwards to 4.
Further overall flexibility increases their efficiency and reduces the need for stopping the control starting now of tools.
The amount of Axes?
Engineering responsable
We have already mentioned the several axes in this article. But shall we make it totally clear what each means.
3-axis generator
A 3-axis top to bottom mill means that the table can move in 2 directions – Back button and Y. This specific permits positioning the workpiece relative to the cutting tool while the distance remains the same. So the 3 rd, Z-axis, is extra by allowing to lower the reducing tool.
CNC remotes permit simultaneous movements of three, providing the necessary overall flexibility for most control needs.
4-axis generator
A 4-axis generator has all the 3 axes as previously described. Although another one also comes in – the A-axis. Now the stand can rotate throughout the X-axis, allowing face milling the factors without repositioning of the workpiece.
5-axis generator
As you can guess, all of that was true for the 4-axis generator also applies to the 5-axis one. Nevertheless we add the B-axis which gives rotational movements around the Y-axis.
5-axis CNC engineering centres cost far more than the other options but make it possible to generate very complex elements in one go. No extra setups are necessary even though the tool life improves through making the suitable part setting possible.
6-axis generator
6-axis milling machine6-axis milling machine
6-axis CNC milling zones are generally not too common as a result of hefty price-tag. They might be up to 75% quicker than 5-axis machines but the need for such features is rare enough to justify the charges. The video above also shows a comparison of your 5-axis and 6-axis generator.
The 6-axis generator has a immobile worktable and the freedom of movements is allocated for the cutting brain. It might move in 3 directions as well as move around these responsable.
CNC Milling Businesses
Milling is suited to many different features, including threading, chamfering, slotting, etc. This permits for producing intricate designs on a single CNC milling centre with agreeable accuracy. The tolerances for CNC engineering are around +/- 0. 1 logistik.
The creation of the aforementioned features takes a variety of different milling operations:
Area milling
Face milling
Angular milling
Kind milling
Profile milling
Gear milling, and so forth.
Plain milling
Ordinary millingPlain milling
Ordinary milling is also typically referred to as surface milling. By using a horizontal mill, that means the cutting tool’s rotational axis is parallel to the cutting surface.
Area milling are able to use different cutters, wide or narrow, according to the necessary outcome. By using a extensive cutter can bring about fast material treatment when in conjunction with gradual cutting speed, fast feed rate and coarse teeth of the cutter. Regarding course, the surface finish of such cutting may well not meet the requirements.
For that reason, a second step can include a change of tools to use greater teeth. This also requires faster reducing speeds and slow feed rates, so the level of stuff removal per time unit is slow. At the same time, the ultimate finish is more accurate. Thus, the blend of the two makes for a good solution from an economical standpoint.
Confront milling
Face millingFace milling
This functioning uses a reducing tool that has teeth on the perimeters as well as on the end. The tool’s axis is verticle with respect to the made part.
Face milling often uses surface milling, as it could produce more intricate conforms and leaves a nice finish. Teeth on the factors do nearly all of the cutting work while the teeth on the tip care for the surface surface finish.
Angular milling
Chamfer millingChamfer milling
This specific milling functioning let us us create chamfered edges, grooves, and so forth There are several ways to perform these features.
In the case of a regular 3-axis mill, the use of different blades makes the most sense. These can be dovetail blades to produce curved grooves or simply a mill with a conical cutting go get the chamfering. Note that the two of these are basically the opposites of each other.
The axis of the used vinyl cutter can be verticle with respect or good surface.
Form milling
Kind millingForm milling
This specific type of milling requires special pedaling to make more intricate surface contours. Convex and concave blades are both types of the tooling that find use here.
Form milling really helps to create these surface contours in a single cut. Typically the tools can help create round recesses, round edges, and so forth Typically the tools must have the right variables to own desired final result.
Gang milling is a sub-category of form milling where utilising several blades simultaneously can create patterns.
Profile milling
Profile millingProfile milling
A common milling functioning to produce convex and cavité parts. The process includes 3 steps – roughing, semi-finishing and finishing.
Roughing uses round inserts to the genuine initial work for removing nearly all of the material. Ball-nose conclusion mills will be the perfect fit for semi-finishing and finishing.
These kinds of work will generally benefit from COMPUTER NUMERICAL CONTROL milling, as 4 and 5-axis technology can considerably speed up the functions as well as provide more expensive.
Gear milling
Gear millingGear milling
Yes, milling also finds use for producing different types of gears. Typically the whole process of producing gears is composed of two steps.
First comes products milling. The cloth softness permits causing in the part with more convenience while reaching great tolerances. The things then go through a heat treatment process to solidify the. After that, CNC turning will be in charge of the final outcome.
Ideal Materials
CNC milling can be used over a variety of different materials. Typically the choice, of course, depends upon the requirements. The selection process consists of these steps:
Causing in the part geometry.
Determining the forces acting after the part. CAD software with HORRIBLE addons can hold much help here.
Specifying the stuff properties based on the results.
Building a set of possible materials.
Choosing the one that fulfils the requirements with the bestt rate for cost-efficiency.
Generating sure that the fabric is suited to milling.
So, we may help you with the last step here.
Metals suited to COMPUTER NUMERICAL CONTROL milling:
Mild metallic
Stainless
Tool metallic
Aluminium lightweight
Brass
Materials suited to milling:
STOMACH MUSCLES
Synthetic
Polycarbonate
POM
PTFE
HDPE
GLANCE
After making your choice, it’s the perfect time to choose a reliable manufacturing contractor for the position. If you are looking for someone to help with milling precious metals, you can simply contact our sales engineers.