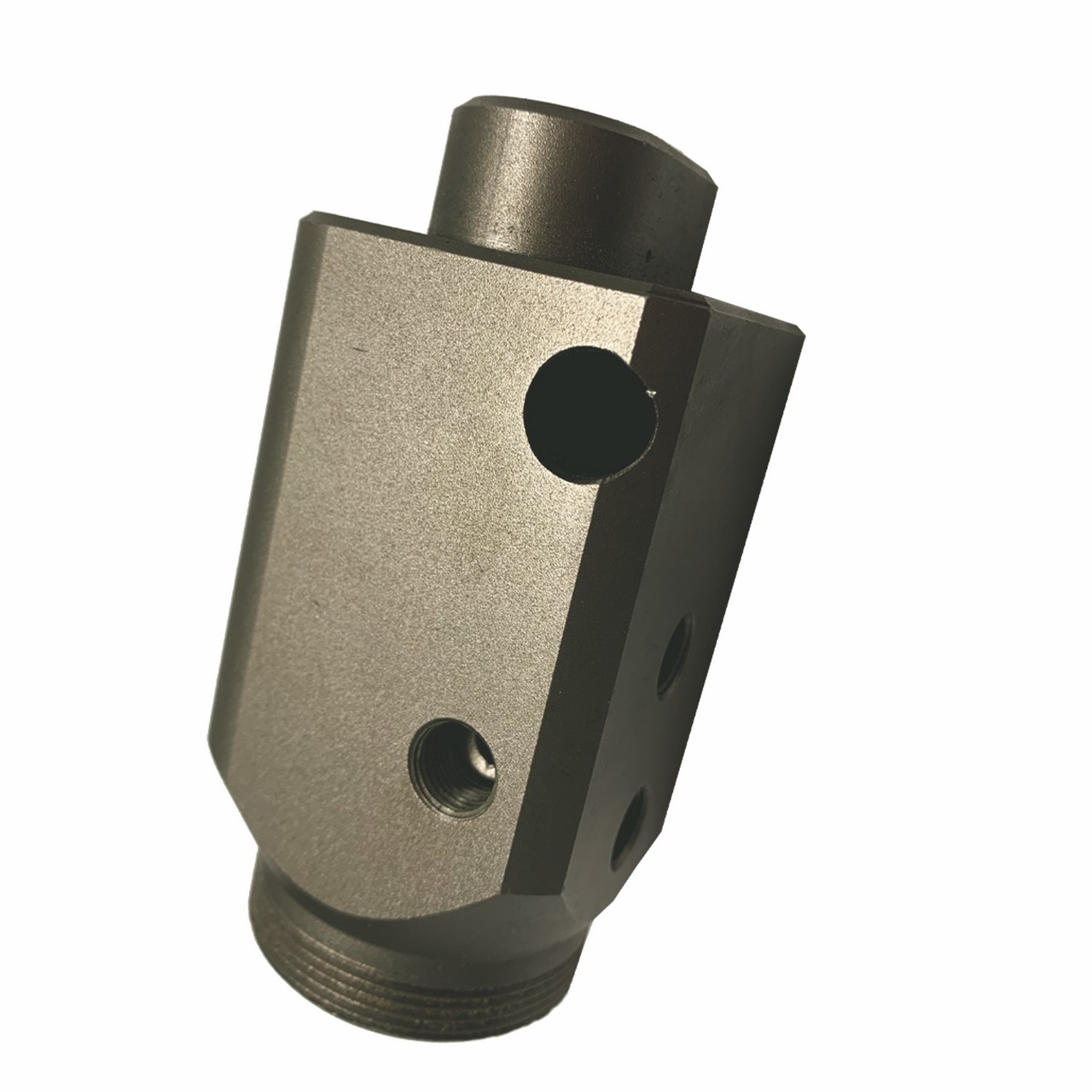
Suggestions about Designing Cost Powerful Machined Parts
ARTICLES
I. ) IMAGES AND PRINTS
2. ) DESIGNING INTENDED FOR ENGINEERING
III. ) LOWERING COSTS IN SETUPS AND FIXTURING
4. ) RAPID PROTOTYPING, STEREOLITHOGRAPHY, FDM, AND SO FORTH.
V. ) VARIOUS OTHER WAYS TO HELP SAVE CASH ON MADE PIECES
VI. ) DESIGNERS CHECKLIST
VII. ) OTHER METHODS
Over time at XIEJIN, we’ve made hundreds and hundreds of parts for hundreds of customers and learned the about how precisely to make parts less costly. Sometimes very small changes in design can generate large savings in part costs. Understanding good part design as it applies to machined parts, and understanding the presumptions machine shops make when you send them a publications will help you to save money, avoid costly problems, to get parts that work well and exceed your targets!
I. ) IMAGES AND PRINTING
Fine parts start out with good prints
We pay attention to what you say and don’t say. We must sell parts!
If you wish the most cost effective part, is considered important to spend a long time on your drawing. Machinists usually tend to think creatively. Remember that your print is the principal communications device in your way on the path to the machinist concentrating on your part. What exactly you want to see in your parts needs to be evidently conveyed in your images. \ to be a professional draftsman to create a good drawing; we possess seen excellent images hand sketched on a piece of copier paper. Just simply make sure that must be clear and has the really basics of legibility (you’d be surprised how many prints don’t! ):
Text should be large enough you just read easily
Lines should be dark and legible
Avoid light grey or violet tones or other colors that would not copy or fernkopie well
Don’t use yellow as a color, it’s challenging to read
Illustration- Here is a properly legible print. Note the careful dimensions with appropriate tolerancing, use of notes, version history, material and finish specification, and many others. The note on who to make contact with with questions could be a compulsory feature in just about any painting!
Illustration- An undesirable publications. Hastily done, very poor default dimensioning, bad color choices, critical features not called out, and so forth You’d be amazed how many prints from professional engineers we acquire that resemble this. Any time ended up saving in this painting will be lost three-fold in the product calls required for clarification and the likely re-do of an incorrect first part. Many retailers will not buy the job when they receive a print similar to this.
Illustration- A reasonable hand-drawn print. Though this print was done via a quick pencil sketch, the result is properly usable. Simple pieces don’t require a fancy CAD painting, nonetheless they do require some attention and clear communication of details.
Give pieces unique names and part numbers
As soon as providing prints for multiple parts, use unique part statistics and clear labels to name different pieces. It is amazing how often this is not done. Avoid using similar names that are easily confused.
Indicate the material you want
We get many prints for parts where the material for the part is not specified. This usually ends up with a call or email rear to the consumer and a delay in the turn-around for the quote. In the event you desire a very specific material, for example a specific grade of stainless steel or aluminum, make certain to specify it (e. g., APPROACH 6061-T651, SS 304L). When you just indicate a material, age. g., “stainless steel”, that’s fine, but understand we will usually find the very least expensive and best to machine class (in stainless, 303; in AL, 6061).
Be specific with material finishes
Should you have a particular surface requirement, make certain to put it in the print (e. g., 32 finish off, etc. ). When you desire a specific component of the part to be soil, turned or machine made, specify that as well. Don’t expect a round part will be changed, often the part will be done on the COMPUTER NUMERICAL CONTROL mill rather than the lathe. Commonly it is more affordable to leave the shop decide the approach to take, so unless you have a specific reason it is advisable to leave the engineering process choice way up to the shop.
You should note that most shops have a certain standard for part completes that you will probably, whether you specify completes or not. Is considered important to understand how a shop views finishing.
Most retailers, including XIEJIN, have found that nice looking parts are better to sell than poor looking pieces, even when both sets of pieces are fully within tolerance. Because of this, shops usually try to maintain a regular surface finish- sanding, nervous-looking, and tumbling (vibratory deburring) parts is common. These techniques remove most tool marks create the parts look better ones. In addition, pointed edges are smoothed and parts are better to handle. Retailers will also usually break sharp perimeters on parts and holes will be lightly chamfered and edged deburred, regardless of if the parts are wheeled or not. Observe that a machine shop is not a jeweler, and that means you will generally still see some small non-critical scratches.
In the event it was a specific reason you desire a sharp border on your part, make certain to indicate it in the print, otherwise you can be rather sure it is deburred and chamfered as a matter of course by the shop. And if you don’t want your parts wheeled or sanded, make certain to specify this. Note pricing may increase since tumbling often reduces side deburring.
Illustration- In the event you look directly at this part, you’ll notice chamfered edges, the best of holes deburred with a light countersink, and precision machined surfaces lightly buffed to enhance the appearance. These are typical “standard practice” completing details often additional by machine stores. Note that not one of these features are on the business print. In case you want something done differently (a sharp edge, for example), make sure to call it away on printed.
Inform us what the part is for and how it is used.
This almost always helps the machinist to understand what a component is for and how it is being used. Doing custom machining is much like a game. You are continually trying to figure out precisely what your customer desires. You win when a finished part works well as well as your customer is pleased with it. Knowing how a component works and what it is for helps greatly in this respect.
When possible, use solid modeling to create complex part design
Using a modern solid building CAD system (such as Solidworks, Professional Engineer or Inventor) can help, particularly if parts have complicated 3D surfaces or features that are hard to see in a 2D sketching. Additionally, we program directly off the outside surfaces when doing 3D engineering of many components. In this instance, having a solid model can save a huge amount of time any money since we don’t have to recreate the model ourselves from the 2D information.
Illustration- Are you able to inform what is heading on with this part in line with the SECOND drawing views
Illustration- With this THREE DIMENSIONAL model, the part geometry becomes instantly obvious. Complex bent shapes also give themselves well to 3D modeling.
Offer a dimensioned or semi-dimensioned 2D printing, even when using solid modeling
There exists a trend among technicians to provide just a solid model to a machine shop. This is an attempt to save time, since in certain CAD systems, like Solidworks, information on holes and other attributes can be shown in the design tree of the solid model. If the machine shop has this license for the software in-house, they can make reference to the design tree and theoretically machine the business with no comprehensive 2D drawing or print at all.
While this seems good, in practice it doesn’t work perfectly. A page of paper is still a lot more convenient than a computer, even a laptop. You’d be astonished what sort of paper drawing is carried around the shop and known to as the task moves from machine to machine. Whenever at all possible, supply an in depth printing with the strong file.
Remember that for complex parts, sometimes you don’t need to fully fine detail the print. A few features, especially complicated 3D surfaces and natural surfaces are extremely hard to dimension in a 2D sketching. Since we program the tool pathways directly off the part geometry anyhow, we really merely have major dimensions, critical dimensions with tolerances, notes on features, etc., in our detailed print.
If designing using the pc, make sure part angles in your CAD files match the dimensions shown in the corresponding images.
Don’t design an element “visually”, and adding dimensions which may have minimum connection with the computer geometry. In the event that we get some type of computer file, unless were specifically warned to the contrary, we always assume the business geometry is dimensionally correct. Often assume the machinist will be encoding off of the computer part geometry. Avoid the urge to revise a dimension in your drawing while expecting to revise the solid model “later on”.
Naturally, with hand-made images, the dimensions take precedence.
Use the drawing title stop to advantage
Load out those items in the drawing subject block, including Stuff, tolerancing and surface finishes. Use the revising blocks if changes are increasingly being made.
Illustration- Here’s a reasonable title block, with a good package of useful information provided. Avoid the temptation to make use of the CAD system non-payments. A few minutes adding real information are going to pay dividends later on.
Look closely at tolerancing, we do!
Shell out attention to how many decimal places you use when calling out a dimension. It is amazing how many drawings we have where the subject block plainly identifies tolerancing based on the number of digits shown after the decimal point (e. g.,. 00=+-. 010″,. 000= +-. 002), nevertheless the person creating the attracting just uses the default number of decimal places (usually three to four places). This specific means every aspect shown seems to require the top precision! The machinist can’t afford to have a part rejected, so minus the proper information he / she will attempt to make every aspect on the part to the required tolerance. Obviously this will create a VERY expensive part. Be sure to spec high tolerances only where you truly need them.
A similar thing applies to bond call-outs. Don’t put a thread patience (e. g., H3) if you really signify it and expect to check it. In my a lot of machining, I can only think of a several conditions where a specific thread tolerance was actually justified. In most all cases, just “8-32” is enough said. (If the tolerance is not specified, we use the most frequent tolerance taps).
Illustration- Considered one of the most frequent mistakes is causing the default CAD dimension precision collection, as is shown here. This will ending up being a costly part, since without other information the machine shop will endeavor to hold high tolerances on every feature. Don’t autumn into this mistake!
Dimension constantly from the same perimeters or datum point
Dimension your part’s features coming from a sole point or datensatz (fachsprachlich) (eg, the area of two easy-to-locate outside edges on a square part, or the centre of a sizable hole). Don’t, for example, dimension one feature from the kept edge, and another from the right edge without rhyme or reason. This kind of can lead to tolerance “build-up” which is generally bad practice. Remember, a machinist will usually be choosing two perimeters of an part (or the biggest market of a hole) setting the A, Y zero of his machine. All of features in that setup will be machined from on this same absolutely nothing location. Dimension your print the same way.
Don’t indicate the tap punch size on printed out
Many modern CAD systems have a fairly easy default hole sorcerer which automatically inserts the faucet punch size for the tapped hole pulled. Avoid using this unless you know just what you are doing. Just indicate the thread desired. It is much better normally to let the machinist decide the tap into drill size and regardless of if the hole will be roll or cut tapped, or even threadmilled. Quite a few factors can have an impact on this choice, including the sort of tap and material, the textile hardness, the self-control, the size and depth of the hole, and so forth For example, roll tapping is much more cost effective for small holes in 6061 aluminum when strict tapping over a COMPUTER NUMERICAL CONTROL machine. When you indicate a tap punch size on printed out, you may drive the machinist to choose between an increasingly expensive and less regular way to choose your thread, or ignoring your observe altogether. It’s likely the individual will call both you and waste both your time. Unless it really matters, leave the tap punch specification up the machinist.
II. ) DESIGNING FOR ENGINEERING
Designing parts that are super easy to machine can make a big difference in part cost and quality.
Make sure inside corners take into account endmill radii.
Try not to design sharp, sq inside corners. Let for the radius of the endmill. If you must have a jean pocket with sharp sq corners, it is possible to complete this task (broaching, EDM, etc. ), nonetheless they are usually much more expensive than simple milling.
Illustration- It is very easy to create square pockets including the example on the left above, but it is harder to machine them than you would think. An ending mill will always leave rounded inside corners, as shown in the right hand version. Some sort of smaller endmill can minimize the radius, but it will probably still be there. Incredibly square corners can be created through other techniques (broaching, EDM, etc. ), but this receives pricey.
If you are fitting something inside a jean pocket, often the four corners can be lower away with an endmill so that the sharp four corners of the matching part will still fit without ruining alignment.
Illustration- Usually, pocket corners can be cut away so that a mating square part can easily still fit effectively in the jean pocket.
Watch EM period to diameter.
Endmills might be best when they are incredibly rigid. Avoid making deep pockets or inside corners with small radii. Commonly, an endmill will cut easily with a length of up about 4 times its size. Endmills can be cut deeper, sometimes up to 10 to 15 times the size, but this receives progressively harder and more time taking in to do. That these cases, the mill must be “stepped down” the wall of the pocket in very small increments, or run at extremely slow rpm and feed rates. Throughout general it is best to reduce pocket depth to as small a multiple of ending mill diameter as possible.
Illustration- Some sort of deep pocket with small inside four corners cut with an extra long endmill is definitely asking for trouble. Endmills like this will gossip and break easily, and surface finish off will be very poor.
Illustration- A great way to work around the above problem would be to accumulate the part from several components. This way the pocket could easily be machine made from the inside side and all corners could be kept sharp.
Approach parts for standard EM sizes; make corners bigger than EM diameter
Like CNC milling is now more common, retailers have tended to use standard size endmills for much of the milling work. This is because modern COMPUTER NUMERICAL CONTROL milling machines can mill arcs and curves without consideration to endmill size. Before CNC, over a manual mill, you might have to choose an endmill with the diameter of the inside area you wanted to mill, or use a difficult-to-setup rotary table. Now practically any radius can be milled with a standard size endmill. For productive material removal retailers still need endmills of different measurements, several shops keep a good offer of the particular common sizes. These are generally usually even domaine of an in, e. g., 1/16″, 3/32″, 1/8″, 3/16″, 1/4″, 1/2″, 3/4″, and so out Metric sizes in even mm installments are common as well.
When planning parts, it is good practice to create inside corners with one of these endmills in head. Yet , when possible don’t pick area radii that are the same as endmill diameters. The reason is that if you bring a. 25″ diameter endmill into a area of. 25″ for example, the endmill has a sizable component of its surface area talking to the work during the finish pass. This results in the endmill at risk of chatter and very poor surface finish. Is considered better to machine a. 300″ size corner with a smaller endmill, such as a. 250″ diameter. If you need something near a. 25″ size corner, choose a rather bigger radius instead, say. 29 or. 30. Keep away from small differences, as a. 251 area will effectively machine much like a. 300 corner. You need to add. 020 or. 030″ to lessen the surface area contact sufficiently.
Illustration- In case the corner of the pocket is contains the same radius for the reason that endmill, there is a sizable area of surface contact on the finish pass (shown in red). Designing a rather larger area over a standard endmill size limits the surface contact and reduces potential gossip.
Don’t specify too deep tapped gaps
Putting threads in holes (tapping) is usually not a horrible process. But it gets progressively more difficult and expensive as the drawn on holes get greater. Keep in head that for maximum strength, you only desire a hole to be tapped to a depth of 1 to at most 3 times the diameter. Virtually any deeper and the screw will bust prior to threads yank out. Take into account the average commercial nut on a bolt. Typically the thickness of the nut is usually is merely 1 to at least one. 5 times the bolt diameter, because this is the thickness that is needed. But naturally, we often see prints with very small holes tapped to extreme depth.
Tolerate in mind too that the threaded component of taps is a couple days and nights. A 4-40 tap into, for example, only has 5/8th of an inch well worth of threads on it. If a deeper threaded ditch is specified, the tap shank should be ground back. For the reason that of the interesting depth of the ditch there is also a long threat of breakage. A really expensive hole to manufacture indeed!
So that you can have a long through hole to clear, for case, a threaded the whole length, try to indicate threads on only one side of the hole, with a drilled ditch from the other end.
Illustration- Longer tapped holes (A. ) require custom tooling and are expensive to make. Instead, design faster holes tapped from each side (B. ). A through drilled hole, good results . short threads from each ending is also acceptable (C. ). If you need to go away a long securer or part through the threaded ditch, consider back monotonous as shown in D.
Watch for High walls- NO ANO DE, toolholder and spindle clearance issues
A further problem area in machining is tool, toolholder and spindle clearance, especially near to high walls or other part features. The ending of an standard ER-16 encolure chuck, which is often used to hold smaller endmills and drills, is about 1. a hundred and twenty-five inch in size. If you have a pocket next to a high wall, for example, this clearance can present a problem. Sometimes a smaller chuck, such as an ER-11, can use. Nonetheless this will still have a size of about. 75″, and will carry quite small tools up to about. 25″.
You must tolerate in mind these tooling clearance issues when making pieces. As always, there are work-arounds, nonetheless they are expensive and frustrating.
When possible, design multiple components or pieces that can be attached, fit, or welded together to reduce clearance issues.
Illustration- The picture shown is a typical machine tool spindle with an endmill holder. The enclosed illustration shows typical toldholder and spindle sizes. These amounts are approximate and will vary with the specific machine tool, taper size (#30, #40, #50), and so on, however they give you an appreciation of types of clearances necessary for easy machining.
Limit Engineering Risk Factors- Style simple parts
A crucial but little brought up factor in part expense is the chance involved in the work. For example, if a shop is going to engrave text on a $20, 1000 mold cavity given by the customer, they will fee many times more than if they are asked to engrave the same text on a $10 piece of steel. Associated with chance. The shop can not afford to make a mistake on the mold, so they will spend much more time testing and demonstrating out your procedures than on the cheap item of steel. Inside addition, whenever they do make a oversight (and mistakes are portion of the business of machining) on a costly mold, it will mean an expensive insurance assert or worse. While such, the shop charges reduced.
Typically the logic follows if a part will get too valuable. Think about a part with countless features designed out of a huge block of aluminum. The only part might take days to make. When the shop makes a mistake close to the finish of the project, the business might have to be scrapped at huge cost. As a result, the shop will charge reduced. If the same part where made of several smaller and less complicated parts bolted with each other, the project would are cheaper, even though the shop now had to produce a larger quantity of parts.
Usually of thumb, it is best to design devices out of simple, smaller parts than to attempt to make a single large complex part.
Illustration- A complex part as shown might much better designed as three individual parts fastened with each other with shoulder mounting bolts or screws with locating pins. Each one of the individual parts then become less dangerous, clearance problems are avoided, and substantial material is stored as well. Frequently the three easier parts will be much less expensive to manufacture than the usual single more complicated part.
III. ) SAVING CASH IN SETUPS AND FIXTURING
Workholding and fixturing is often one of the most expensive parts of the machining process. Apart from designing parts that are super easy to machine, it is very important to develop parts that are super easy to hold.
Style for Vise fixturing (size limitations, and so on. )
Among the most typical and most affordable workholding devices at the mechanic is the Kurt brand milling vise. The vise is a accuracy tool most commonly with jaws 6 inches wide, one 75″ deep and capable of starting about 9 ins. It is floor flat and seite an seite to 2 ten-thousandths of an in ., and is able of both great precision and great speed in launching and unloading components. However, to help make the easiest and cheapest use of a milling vise like this, parts need to have parallel sides that can be gripped in the vise jaws. Whenever possible, design components with some grippable parallel edges which can be held in a milling vise.
Illustration- A Kurt-style vise is the most typical workholding device at the mechanic. The most common of these vises have 6″ long jaws which open about 9″.
Design more complicated parts for softjaw fixturing
When components don’t have seite an seite edges (e. gary the gadget guy., round, disk-like parts), we often use softjaws in a Kurt vise to hold them. These types of jaws are reduce away at the very top with the form of the part, the business is positioned in the precision machined recess and stiffened. Although this fixturing strategy is not quite as cheap as using hard jaws since there is an additional machining step, it is a convenient and relatively cheap way to go. This still requires parts that can be squeezed from the sides to be held.
Illustration- Machined aluminum softjaws, such as in a 6″ Kurt double vise, are a common way to hold small parts without directly sides.
Avoid multiple setups when possible
The least expensive parts to machine are that can be completed in just one setup, i. e., they do not have features on the edges or on the back that need the parts to be flipped as well as repositioned. Extra setups add substantial time and cost to parts. Prevent them when possible.
Some simple features, such as counterbores and countersinks, can be carried out freehand on a drill press or manual mill. Given that a costly CNC machine does not be setup for the rear side, this might not add much cost. Also, components can sometimes be run on a machine with a CNC 4th axis rotary table, which can eliminate some manual setups, but this is usually applicable simply to higher volume parts.
Illustration- The first image is a simple, one-setup part. Yet add a wallet on the back again, also it becomes a two-setup job. Include holes quietly, and it is 3 setups, unless the volume is high enough to warrant use of a CNC 4th axis table.
When to stick down components with mp3
An additional common way of fixturing entails sticking down material for slim parts with double-sided tape. This can work nicely with plastic materials and other materials that do not require flood coolant. It does require that the components have a reasonable amount of area on the back again therefore the tape keeps well, and even then you are not able to mill heavy components out of hard materials since the tape is not strong enough to keep them securely. Cleansing the residue from the adhesive may also sometimes be a difficult job, so this strategy is usually avoided if the parts can be screwed down or otherwise fixtured.
Provide through openings for screw down fixturing
With bigger parts, especially plate-like parts that can not be kept well in a vise, we often screw the pieces down to a set fixture denture. In case the outside of the part should be machined, which is usually the truth, it is nice to have some through holes to put hold-down mounting bolts through. Sometimes existing screw holes particular in the business can be used, but other times it is convenient to add additional holes. If attach down holes may be added to a significant part, it is nice to observe that on the print. It often helps you to save considerable time in fixturing.
4. ) RAPID PROTOTYPING, STEREOLITHOGRAPHY, FDM, AND EVEN SO FORTH
In the event that you have low volume, high intricacy plastic parts to make, it could be well worth considering Rapid Prototyping. Rapid Prototyping, or RP, is a general term for producing 3 dimensional models from CAD files using totally automated equipment. Elements are generally created from plastics or polymers making use of several methods, including stereolithograpy, lazer sintering, and joined deposition technologies (FDM), and others.
With Speedy Prototyping, cost can sometimes be less for small volumes of complex elements (a good example is making intricate prototypes of elements that will be injection molded in production). The most effective elements for RP are those which may have the lowest material volume (e. g., hollow elements with thin walls) and a high level of depth (lots of features). This is because the expense of RP elements is far more dependent on part size and volume than on complexity.
RP materials are relatively expensive, so parts with lots of amount get pricey. Engineering is also much faster than RP in most circumstances because material can be removed much more rapidly than RP material layers can be added. RP parts require first deposit of a huge number of very thin layers to construct part detail. Consequently, build times for parts can be long, limiting generation applications. However, because production is totally automated and intricacy is not an issue, parts can usually be overturn quickly. Also, some parts can be produced with RP that are almost impossible to produce through traditional developing, such as exemplified assemblies.
Generally RP is not used for quantity part production, due to the relatively long build times (CNC machining, molding, or other manufacturing methods may be better suited in this case). Other constraints add a limited choice of materials (e. g., plastics only, commonly ABS or polycarbonate plastic for fused deposition technology machines), difficulty with small threaded holes thanks to resolution limitations, a relatively small build envelope (8x8x12″ or 203x203x305mm is common) and constraints in wall fullness (. 020″ or. 5mm is common). In addition, although RP parts can be reasonably exact, they still do not reach the level of accurate of CNC engineering.
V. ) VARIOUS OTHER WAYS TO HELP SAVE CASH ON MADE ELEMENTS
Small increased partly quantity can make a huge variation in per-unit cost
Per-unit part cost is very hypersensitive to the quantity of elements run. Sometimes a customer can’t appreciate how a single part could cost 300 dollar when 10 of the same part may cost 50 dollars. The reason is usually lies in setup and encoding. CNC machines are incredibly fast and useful at producing elements when they are running. With small parts, the run time (the time the part is definitely being cut by the machine tool) is usually short- normally a very few minutes or less. However, usually it takes an hour or more of encoding plus two several hours of setup (getting vises placed, a fixture made, reloading the machine with tools, offsetting tools and finding work coordinates, proving out your program, etc. ) for even a not at all hard CNC part. Inside our example above, suppose the part takes 1 hour to program (@ $75/hr), two hours to setup, 10 minutes to perform and a few minutes to deburr, clean upwards, and so out Let’s call it 3. 5 several hours of labor, at $75/hr that means $262. 50, plus material cost (with shipping costs), and the overall part cost nears $300. At this point imagine there are 10 parts. Inside this case, we have a little more toil in deburring and tidy up, let’s call the overall labor (less the run time) numerous hours vs. 3. 5. That is $300 at $75/hr. Add in hundred minutes of run time (10 minutes each of twelve parts), and you have $425. Put material cost of a few money an element, shipping, and so forth. and then youre at about 500 usd. Hence the 300 dollar or $50 part.
Usually (and again there always are exceptions), the programming and create costs are relatively fixed over a certain variety of elements. These costs are a huge proportion of the total part cost in small quantities. They get small amortized over large quantities. Inside the example above, the initial 300 dollar programming and create cost is less than $1 for every part at volumes over 300. Inside this case, the run time becomes more critical, since the actual cost of the machine cutting now becomes the most costly aspect and the limiting factor for cost. Due to the fact eventually the COMPUTER NUMERICAL CONTROL machine cannot be optimized to piece any faster, the run time for every part becomes a constant, and the part cost truly does not fall far more for higher variety.
To sum upwards, for the minimum per-unit cost, make an effort to increase part quantity, even by a tiny range. Even a bounce from one to two or a few units can produce a considerable variation in per product cost. The top per-unit savings are usually found by increasing volume at low part volumes, at higher volumes, the per-unit cost doesn’t drop as fast for the increase in volume.
Illustration- As this chart illustrates, nearly all of the decline in per part cost occurs at the reduced conclusion of the quantity scale. Perhaps a growth of one or two products ordered can significantly decrease per product cost.
Part people can also reduce costs
Often, at the very least part of the setup and encoding time can be saved if several similar parts are ordered concurrently. Typically the way many elements are programmed, it will be quite simple to leave out or add additional features to parts. Because similar parts are often fixtured the same way (e. h., using the same softjaws in a vise, or the same screw-down plate), the expense of setup is significantly reduced as well. Part people regularily use similar tooling, so many tools can be re-used without having to reload and re-offset them in the CNC machine.
If you are working on many different variations of similar parts, it is better to hold back until you have done several parts and get for a price on all of them simultaneously. Observe that in this case, the price you receive will be for all the parts bought at once- if you order merely a single part from the group the business will need to be requoted.
Go sparingly on high-tolerance features
A person of the best ways to save cash on made parts is to be careful to specify high tolerances only when you really need them. If the outdoor of a certain part is, for case, merely a cosmetic vision surface, please contact us. Don’t use the default CAD system dimensioning on everything. If some features only desire a +-. 020 accuracy as opposed to +-. 002, take the time to put that in your print. That will definitely topple some cost off the part.
Keep away from specifying high flatness for thin materials. We frequently see things like a. 0005″ flatness specification for large, thin metal or stainless plate designs. It is very expensive to endeavor to make pieces to these kind of tolerances, and large, slender sheets of materials like AL or stainless can not be trusted to maintain their tolerances after a while. There is a reason that surface plates are constructed of 4″ thick granite.
As well, avoid putting no tolerances or special notes on gaps something is suitable into. If a particular pocket presents a cavity for a precision impact press-fit, make certain to mention that on the print. Because of this the hole is sure to find the attention it needs from the machinist.
Treat your machine shop professionally
In the event you want the best out of your machine shop, it’s important to treat them well. People like to do business with people they like, and it is an acronym to reason that favorite customers get special attention. Below are a few do’s and don’ts regarding machine shop proprieties:
DO converse regularly with your shop, call them if you see problems. Don’t let problems simmer. Carry out work along with them to resolve issues rather. Cutting metal to high tolerances is definitely a difficult art, and many mistakes are inescapable.
DO talk to with your shop on design issues. Until you’ve spent numerous your life working as a machinist, don’t assume you know read more about manufacturing issues than they do. Virtually all professional machinists have many numerous training. Quite a few have advanced diplomas. Treat them as peers, not as subordinates.
DO pay your bills on time. Nearly all shops pay in close proximity attention to this. You cannot find any question that fast paying customers get treated better.
DON’T use your shop as a free quoting in order to opportunity out the price tag on recommended projects. Quotes are expensive for a store. Only ask quotes for job opportunities the shop has a good possiblity to getting. Don’t quote out and about jobs to more than 2 or 3 shops. Would not expect a shop to remain to price multiple jobs without winning some work.
DON’T try to beat a store down on part costs. Do ask design advice how part costs can be reduced. Cure your shop as part of your manufacturing team, and foster communication between design and making.
VI. ) MAKERS INSIGHTS
Detailed Printing:
Printing evidently inteligible
Multiple views shown (3D if possible)
Careful dimensioning and tolerancing provided
Product particular
Finish particular (if desired)
Aspect numbers assigned to parts
Revision record shown.
Part purpose evidently identified
Possesses CAD format data file been given
Does indeed CAD file match dimensioned publications
Design and style Issues:
Inside four corners rounded to consider endmill diameters
Depth of pockets not increased for endmill period
Deep pockets with small inside radii avoided
Holes not tapped too deeply
Clearances presented to spindle and tools
Parts are easy to light fixture
Setups minimized
Other:
Class parts in similar families
Maximize volumes of prints for per-unit cost reduction
VII. ) OTHER METHODS
Net discussion forums can be an outstanding source of information. Anthony, a prolific cartel and knowledgeable making professional (who hopes to remain anonymous) created an outstanding set of the way to reducing the price tag on machining. With his permission, I've created a link to it here: Anthony’s The way to Cost-effective Aspect Design