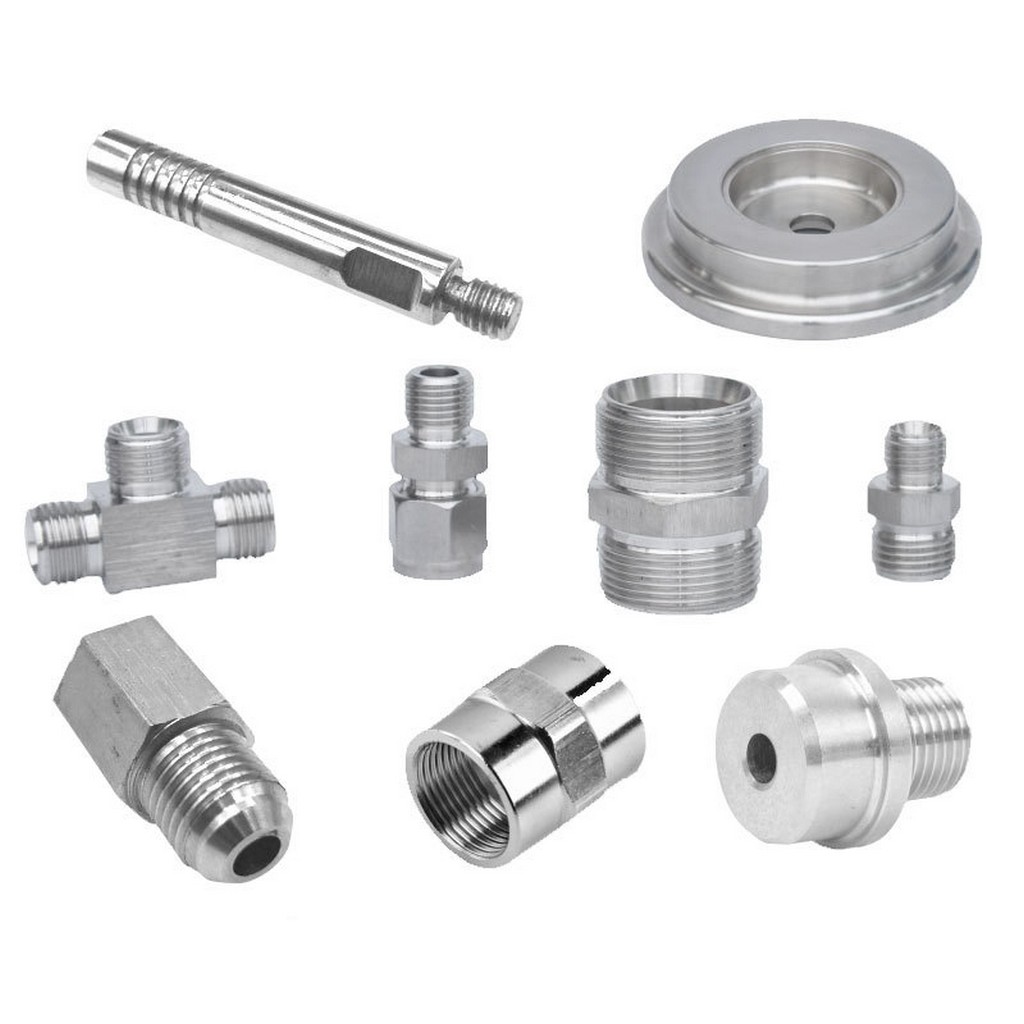
Expense casting is amongst the oldest manufacturing processes, dating back to again centuries , in which often molten metal is poured in to a expendable ceramic mold. Themold is formed by simply by using a wax pattern-- a disposable piece inside the state of the desired part. The pattern is surrounded, or "invested", into ceramic slurry that stiffens in to the mold. Investment casting is generally generally known as "lost- polish casting" such as the wax pattern is normally melted right out of the mold after it had been formed. Lox-- wax processes are one-- to- one( one design creates one part), which raises production time and costs on accordance with other casting procedures. However, since the mold is damaged along the way , parts with complex geometries and intricate information could be created.
Investment spreading can most metals, most generally using aluminum alloys, bronze metals, magnesium alloys, cast iron, metal steel, and tool steel. This kind of process is beneficial for throwing metals with high melting temps that can not be shaped in plaster or metal. Parts that are typically made simply by investment casting include those with complex geometry including turbine cutting blades or firearm components. High heat applications are also common, including parts for the automotive, plane, and military industries.
Investment spreading requires the use of a metal pass away, wax, ceramic slurry, furnace, smelted metal, and any machines required for sandblasting, cutting, or grinding. The procedure steps include the following:
Design creation- The wax habits are usually injection molded into a good metal die and are created as one piece. Cores might be used to form any kind of internal features on the design. Several of these patterns will be attached to a central polish gating system( sprue, runners, and risers), to form a woods- like assembly. The gating system forms the channels throughout which the molten metal will certainly flow to the mold tooth cavity.
Mold creation- This "pattern tree" is dipped into a good slurry of fine ceramic contaminants, coated with more coarse contaminants, and then dried to type a ceramic shell around the patterns and gating system. This kind of process is repeated until the shell is thick enough to withstand the molten metal this will encounter. The shell can now be put into an oven and the wax is melted away leaving a hollow ceramic covering that acts as a 1- piece mold, hence the name "lost wax" casting.
Flowing- The mold is preheated in a furnace to around 1000° C( 1832° F) as well as the molten metallic is poured from a spoon into the gating approach to the mold, filling the mildew cavity. Pouring is typically accomplished manually under the force in gravity, but other methods many of these as vacuum or pressure will be sometimes used.
Cooling- Following the mold has been packed, the molten metal is allowed to cool and solidify in to the condition of the last spreading. Cooling time will depend upon the thickness of the component, thickness from the mold, and the material used.
Casting removal-- After the molten metal offers cooled, the mold can become broken and the casting eliminated. The ceramic mold is commonly broken using water jets, yet several other methods exist. When removed, the parts are segregated from the gating system simply by either sawing or cold cigarette smoking( using liquid nitrogen).
Finishing-- Often times, finishing functions many of these as grinding or sandblasting will be used to smooth the organization at the gates. Heat cure is additionally sometimes used to solidify the final part.