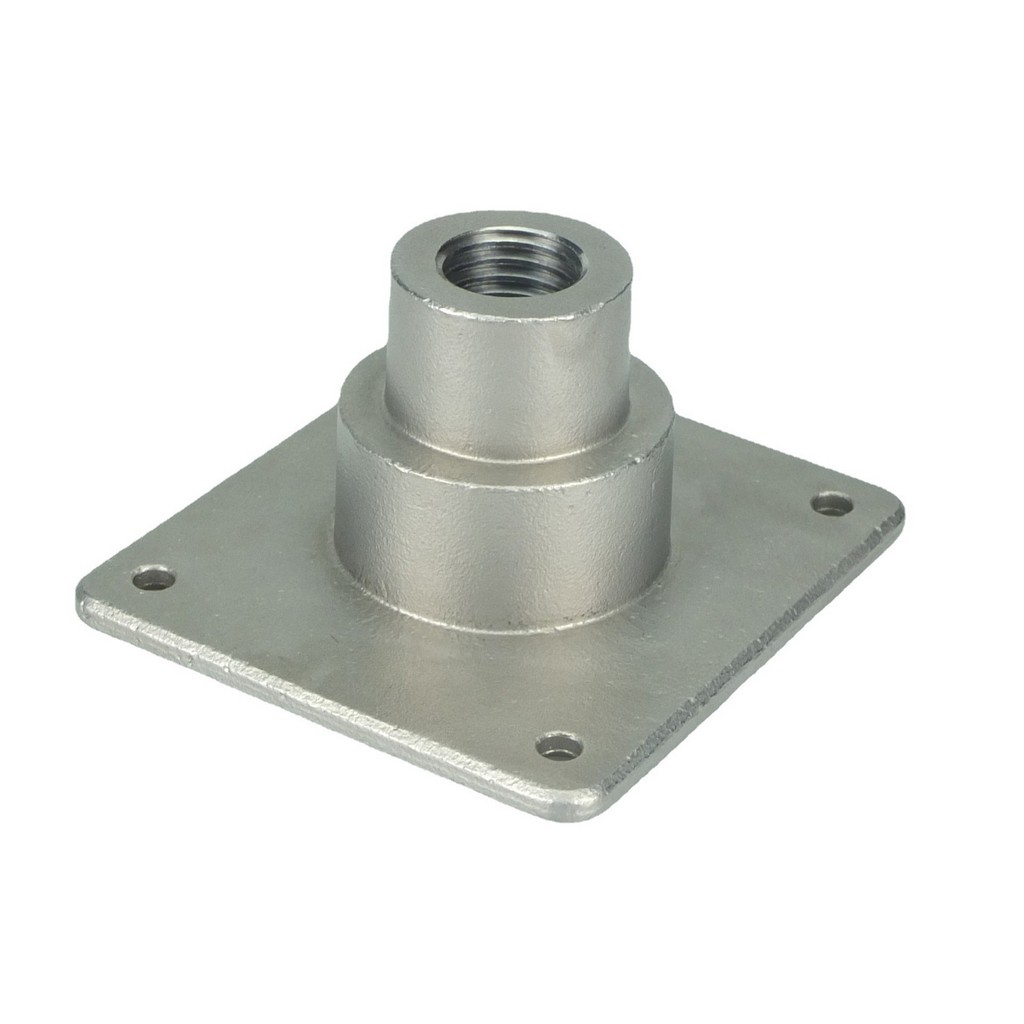
Die casting is a widely used permanent mould metal casting process, in which molten metal is forced into the mould called "Dies" at pressures ranging from 0.7 to 700 MPa, where it solidifies into a metal cast. Die castings, sometimes known as pressure die casting, are used in automotive housings, appliance components, and toys.
Casting die example
Casting die example (source: indiamart.com)
Nonferrous metals aluminium, zinc, copper, magnesium, lead, pewter, and tin - based alloys, are widely used to produce robust, high - quality complex components. Different chemical elements are added to the molten metal to achieve the desired metal chemical composition to satisfy some challenging parts.
Advertisement
Advertisement
Depending on the part's complexity, size and material, the final piece is either single or multiple casts. Dies can have either a single cavity, multiple cavities, several different part cavities, or a unit die in which multiple dies are combined to make a master holding die.
die - casting - die
die - casting - die
The process was introduced in the mid - 19th century to make parts for the printing industry. Since then, it has emerged as one of the most critical manufacturing processes with many technological advancements, such as metallurgical control measures to improve the manufacturing criteria.
As shown below, die casting can produce parts with complex features and an excellent surface finish. It can also compete with other manufacturing techniques such as sheet metal stamping, forging, and other casting processes.
die casting examples
Die casting examples (decardy.com)
Advantages and Disadvantages
Die casting advantages
Die - cast parts are relatively cheaper and produce uniform quality for large volume production. Lower labour costs are due to semi or fully automated processes.
Intricate forms and complex shapes can be cast easily, with part sizes ranging from 25g to 25Kg.
Parts with walls as thin as 0.38 mm are possible because of the high pressure used during the process.
Because the molten metal rapidly cools at the die walls, the casting has fine - grained hard skin with excellent strength. As a result, as the wall thickness decreases, the strength - to - weight ratio of die - cast components increases
Generates smooth surfaces for bearings that would otherwise be machined.
It can generate net shape products at high rates requiring little or no post - processing.
Excellent dimensional accuracy and good surface finish – 0.8 - 3.2 um Ra.
Smaller pieces can be manufactured using either multi - cavity die or miniature die casting
Die - casting - parts
Die - casting - parts (source: Polaris Industries/NADCA)
Advertisement
Advertisement
Die casting disadvantages
Die casting parts are only economical for large production batches due to their high equipment cost
High melting point metals and alloys are not suitable
Because of iron content, ferrous metals such as stainless steel, carbon steel, and alloy steel tend to rust hence not suitable
Large pieces are unable to be cast due to die design and process limitation
High die cost and generally long lead time.
Changes to part design are time - consuming and expensive, hence worth prototyping the part before committing to the die casting
Porosity due to trapped air and gases affects the integrity of the part. Vacuum die casting reduces porosity by creating a vacuum before molten metal fill.
Die casting types
Hot chamber vs Cold chamber process
Hot chamber vs Cold chamber process (source: sunrise - metal.com)
The two basic types of die casting machines are Hot chamber and Cold chamber machines. The variations on these two significant casting process types are vacuum, squeeze, low - pressure and semi - solid die casting. Different die casting processes are chosen over others depending on part material, geometry, size, and complexity.
Hot chamber process
The hot chamber process is sometimes known as the hot die or gooseneck casting process. In this process, the plunger and chamber of the injection mechanism are dipped in the molten metal bath of a metal furnace (Image below) and used for low melting point metals that don't chemically attack the dipped plunger assembly.
hot chamber process
Hot chamber process (source:Kalpakjian & Schmid)
With the dies closed, the plunger withdraws and opens the chamber port to allow the molten metal to flow into the chamber. Then the plunger seals the port while pushing the molten metal into the die cavity through the gooseneck and the nozzle. After entering the die cavity, the molten metal is held under pressure until it solidifies inside the die. The hot chamber process yields a much higher production rate than the cold chamber process because of the high pressure.
Hot chamber casting is better suited to dealing with metals with lower melting points, such as tin and zinc, as well as alloys.
Advertisement
Advertisement
Advantages of Hot chamber die casting
It offers a faster production rate – up to 18, 000 shots per hour for smaller components.
Produces parts with reduced porosity
Melts the metal within the die casting machine
The process produces minimum wastage
Longer die life due to the low melting point
Disadvantages of Hot chamber die casting
Cost - effective only for high - volume production batch
High - melting point metals cannot be used
High - pressure range required
Low metal fluidity hence limited the product's complexity
Heat treatment issues
Ejector marks and tiny amounts of flash at the die separating line may remain.
Cold chamber process
In the cold chamber process, molten metal is poured into the shot sleeve or chamber part of the injection cylinder before pushing into the mould. Because the sleeve is not heated, the procedure is known as the cold chamber process. Since the metal melting pot is separate, it doesn't have a corrosion problem.
Cold chamber process
Cold chamber process (source:Kalpakjian & Schmid)
The cold chamber process starts when molten material is transferred to the shot chamber from the furnace through the pouring hole. Then a hydraulic plunger seals the cold chamber port and forces the metal into the mould cavity at pressure. The pressure ranges between 30Mpa and 150 MPa.
This process is typically used for high - melting - point alloys of aluminium, magnesium, and copper, while other metals including ferrous metals can also be cast. Molten - metal temperatures begin at 600°C for aluminium and certain magnesium alloys and rise significantly for copper - and iron - based alloys.
Advantages of Cold chamber die casting
Higher - strength parts
Denser metal castings due to increased pressure during injection
Lower maintenance cost
It brings exceptional dimensional accuracy to the part.
Possible high - speed production.
Simple - to - carryout process.
Disadvantages of Cold chamber die casting
Slower cycle time than hot chamber die - casting.
It might be due to transferring the metal from the furnace to the chamber.
The level of oxidation and other contaminants remains high in the process.
The quality of the final part is more prone to be affected due to pollutants.
Low - Pressure Die Casting Process
Advertisement
Advertisement
Aluminium components that are symmetric around some axis of rotation significantly support the idea of low - pressure die casting. The wheels of the vehicle are a glaring example of low - pressure die casting. In this type of die casting, the mould remains vertically above the molten metal bath. It remains connected to it with a riser tube. The heated metal is then pressurized from 20kPa to 100kPa in the chamber, pulling the molten metal upward into the mould.
Vacuum die casting
The vacuum die - casting process is an add - on for the two traditional die - casting methods and is most associated with a cold chamber process. A vacuum source removes the air and gases trapped within the die cavity before the molten metal enters the die cavity.
This type of die casting minimizes turbulence and gas inclusions and is beneficial in applications intended for post - cast heat treatment.
Some of the advantages of this casting type are improved mechanical properties, better surface finish, dimensional stability, shorter cycle time, reduced defects caused by the trapped gasses. The parts can also be heat treated
Squeeze casting process
Squeeze casting, also known as Liquid metal forging incorporates features from both casting and forging to make automotive components and mortar bodies. The image shows the operation sequence of the squeeze casting process, where the molten metal is squeezed into the mould while filling up the recessed regions of moulding, which offers hugely dense products at the end of the process. This method is also used to make reinforced metal matrix composites, in which molten aluminium infiltrates a fibre reinforcing structure.
Squeeze casting process
Squeeze casting process (source: open. edu)
Squeeze castings have reduced shrinkage and gas porosity, improved mechanical qualities due to small grain structure induced by quick solidification, and superior surface quality. Aluminium and magnesium alloys are frequently processed via squeeze casting.
Semi - solid metal forming
Semi - solid metal forming (SSM), also known as Semi - solid forming, semi - solid die - casting or mushy state processing is a type of die casting process that incorporates features of both casting and forging and uses semi - molten material.
It is commonly used to make aluminium alloy parts for aerospace, pressure containment, military, engine mounts and blocks, and oil pump filter housings.
They can produce complex parts with thin walls, excellent mechanical properties, superior surface finish, comparably reduced porosity and tight tolerance. They can also be heat treated. One of the disadvantages is that the process is extremely susceptible to environmental factors such as temperature hence manufacturing equipment and the environment needs more control which leads to expensive equipment.
Die casting materials
Although it can cast both ferrous and nonferrous materials, not all materials are suitable for die casting because the process entails heating the material to its melting point and then pressing it into reusable moulds. As a result, the materials such as magnesium, zinc, aluminium, iron, copper, silicon, tin, and lead are more often than not utilised for die cast parts.
Aluminium
Because of the low - cost nature of aluminium, it is widely used in the die casting process. Die casting aluminium is lightweight and environmentally friendly, and it has good dimensional stability, allowing producers to produce components with thin walls and intricate geometries. Aluminium components have several uses in the aerospace, automotive, and electronics industries due to their corrosion resistance and thermal/electrical conductivity. Aluminium is alloyed with silicon and copper to avoid shrinking or shattering at high temperatures.
Zinc
Zinc die casting is a versatile production method that is ideal for items that require increased strength and ductility, high accuracy, tight tolerance, and outstanding thermal characteristics. The most common examples of zinc die casting items are gears and connectors. Zinc may need to be blended with aluminium to improve the final product's quality. Because of this metal's low melting point, zinc die - casting is ideal for hot chamber die casting. Zinc die casting components have several uses in the consumer electronics and automotive sectors.
Copper
Almost all of the items made from copper are durable. Furthermore, copper has high corrosion resistance. As a result, it is widely used to produce components for the plumbing and electrical industries.
Magnesium
Magnesium is an ideal metal for die casting when thin - structured walls and high accuracy are required. It has a high strength - to - weight ratio and is lightweight hence used widely in the aerospace industry.
Zinc alloys
Zinc alloys, such as ZA alloys and Zamak alloys, continue to be extremely easy to die - cast, and their reaction is also ideal for this process due to increased strength and castability. Zinc alloys are widely used as a decorative and practical alternative to iron and brass.
Bronze and brass alloys
Bronze and brass alloys may be die - cast almost as rapidly as zinc alloys. Bronze and brass alloys enable the producer to make durable components with better machinability, particularly in the presence of lead.
Brass alloys also offer good corrosion resistance, a low melting temperature, a low coefficient of friction, relatively high strength due to the inclusion of aluminium, and recyclability, in addition to a completely accurate internal examination.
Lead alloys
Lead alloys are used to manufacture fire - safety equipment, ornamental metal items, and bearings. Without a doubt, it is due to their capacity to withstand corrosion. They are not recommended for use in goods that come into contact with food.