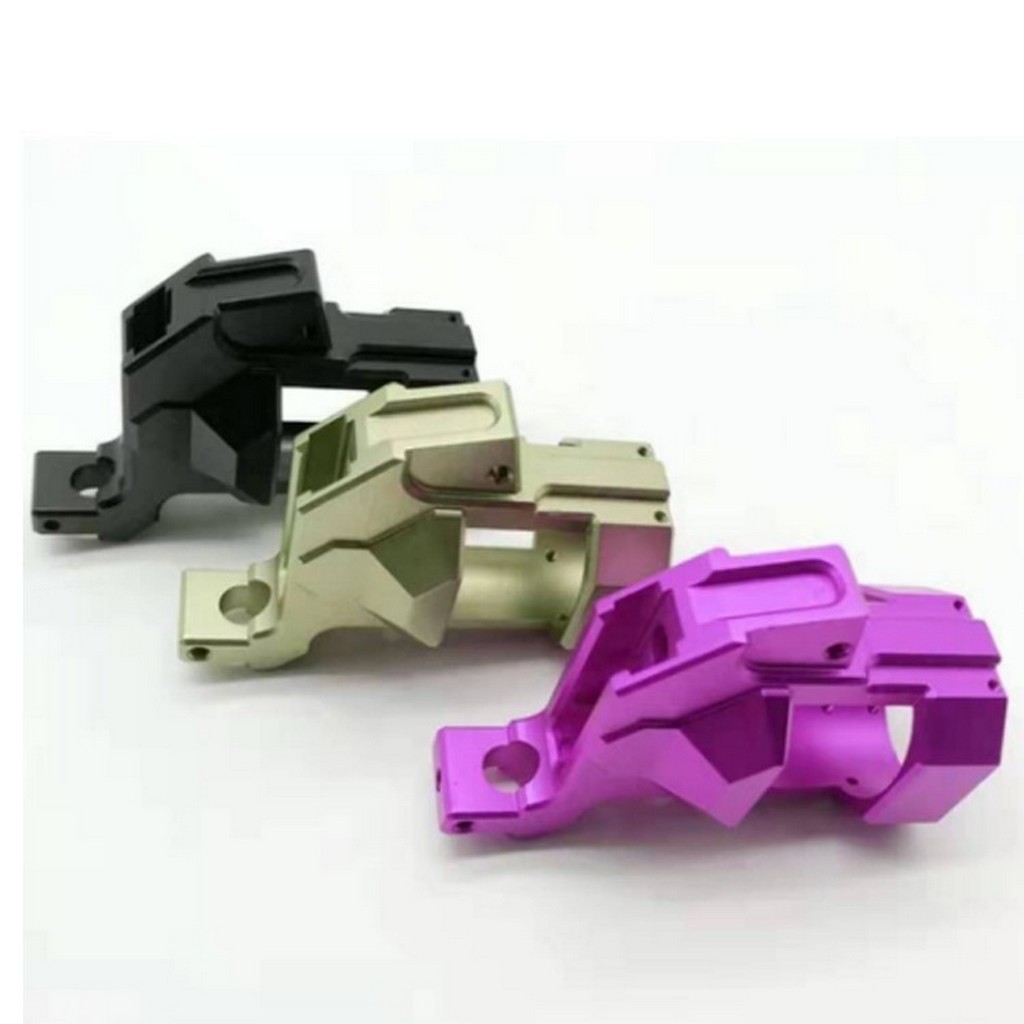
XIEJIN casting is really a manufacturing method which could produce geometrically complex steel parts through the usage of reusable forms, called dies. Conditionsdie throwing process involves conditions heater, metal, die casting machine, and die. The metal, typically a great non- ferrous alloy a number of these as aluminum or zinc, is generally melted in the furnace and next injected to the dies within the die casting machine. You will discover two main kinds of expire casting machines- hot holding chamber machines( useful for alloys with low melting temperatures, such because zinc) and cold chamber devices( employed for alloys with large melting temperatures, such as for example aluminum). Theyvariations between the unit will soon be detailed in the areas on equipment and tooling. Nevertheless, in the machines, following smelted metal is injected into the becomes deceased, it rapidly cools and confirms into the ultimate part, the casting. Steps on this technique are described on more detail in these section.
Pass awaycasting hot holding chamber machine overview
XIEJINcasting warm chamber machine overview
Pass awaythrowing cold chamber machine summary
Expire casting cold chamber machine summary
The castings that are made in this technique may vary greatly in proportions and weight, varying from one or two ounces to 100 pounds. One common software of die-cast parts will soon be housings- thin- walled enclosures, often requiring many steak and bosses on the space. Metal housings for a variety of appliances and equipment will often be die-cast. Several automobile parts are produced using die throwing, including pistons, cylinder heads, and blocks. Other common die shed parts include propellers, gears, bushing, pumps, and valves.
Go back to top
Abilities
TypicalFeasible
Designs: Thin- walled: Complex
Sturdy: Cylindrical
Solid: Cu
Solid: Complicated
Toned
Thin- walled: Cylindrical
Thin- walled: Cubic
Component size: Weight: 0. 5 ounce- 500 pound
Materials: Alloys
Aluminium
Business lead
Magnesium (mg)
Container
Zinc
Water piping
Surface finish- Ra: 32- 63 μin sixteen- 125 μin
Tolerance:± 0. 015 in.± zero. 0005 in.
Max wall width: 0. 05- 0. five in. 0. 015- a particular. 5 in.
Quantity: 10000-- 1000000 1000- 1000000
Business lead time: Months Many weeks
Features: Will produce large parts
Mightbuild complex shapes
Largepower parts
Greatsurface finish and accuracy
Largeproduction rate
Lowerlabor price
Discardmay become recycled
Disadvantages: Trimming is necessary
Highertooling and equipment price
Minimaldie life
Lengthybusiness lead time
Applications: Engine components, pumping components, appliance housing
Match facing:
Proceed
Disclaimer: All process specifications reveal the approximate array of an excellent process 's abilities and really should become viewed only as a tenet. Actual abilities are influenced by producer, equipment, material, and part requirements.
Go back to best
ProcedureCycle
The method routine for die casting includes fitness main stages, that are described below. The whole cycle time is normally very short, typically between two seconds and 1 minute.
Clamping- Step one could be the preparation and clamping of the 2 halves of the expire. Each die half is initial cleaned from the prior shot after which lubricated to ensure that the ejection from the upcoming part. How manylubrication time raises with part size, as well as how many major and side- cores. Likewise, lubrication may not be needed after each and every cycle, but following a few cycles, with regards to the material. After decrease in friction, both die halves, which is attached in the die casting equipment, are closed and securely clamped together. Sufficient force must become placed on the die to continue to keep it securely closed as the metal is injected. Enough time needed to close and clamp the die is dependent upon the device- larger devices( individuals with greater clamping forces) will demand more hours. This sort of time may be estimated from the dry cycle efforts in the gear.
Injection- The smelted metal, that is maintained in a group temperature inside the furnace, is next transferred right chamber where maybe it's shot in to the die. The thought of transferring the molten metallic depend upon which kind in die casting machine, if the good hot chamber or cold holding chamber machine is used. The with this equipment can be detailed next section. Once transmitted, the molten metal is inserted at high pressures in to the die. Typical injection pressure runs from 1, 000 to vinte, 000 psi. This pressure supports the molten metal inside dead during solidification. The total amount in metal which is injected inside the die is the filmed. Enough timeinjection time is the full time necessary for the smelted metal to fill all inside the channels and cavities within the die. Now can be extremely short, typically significantly less than zero. 1 seconds, so that you can prevent early solidification of almost any one the main steel. The appropriate injection time may be easily determined through thermodynamic houses of the fabric, as well as the wall structure thickness of the casting. A more substantial wall thickness will need a good longer injection time. In case the place where a cold holding chamber die casting machine is now used, the injection time should also are you a chance to yourself ladle the molten metal in the shot chamber.
Cooling-- The molten metal that could be shot in to the die will quickly cool and solidify in order to enters the die tooth cavity. When the complete cavity is normally filled as well as the molten metallic solidifies, the ultimate form inside the casting is created. The die can't be opened before the cooling time offers elapsed plus the casting is solidified. Probably the mostcooling time can be estimated from several thermodynamic houses in the metal, the absolute most wall structure thickness from the casting, along with the complexity in the die. A great greater wall thickness will be needing an extended cooling time. The extrageometric complexity in the expire also needs a longer chilling time since the extra amount of capacity the flow of heat.
Ejection- Following the established cooling time has transpired, the die halves may be opened and an ejection mechanism may push the casting out within the die cavity. You an excellent possiblity to open the XIEJIN could be estimated through the dry cycle moments of the gear plus the ejection time is normally based on the dimensions of the casting 's envelope and includes period for that casting to fall season free from the die. The ejection mechanism must apply several force to eject the component because during cooling the portion shrinks and adheres for the die. After the casting is normally ejected, the die can turn out to be clamped shut for the next injection.
Trimming- During chilling, the items inside the stations from the die will set attached with all the casting. This extra material, along side any expensive which includes occurred, must certanly be cut from your casting either yourself via cutting or sawing, or simply employing a trimming press. The full time needed to trim the surplus material could be approximated from how big the casting 's envelope. The scrap materials that comes from this removing will either be discarded or are always reused inside the XIEJIN casting process. Recycled material may choose to be reconditioned to the right chemical composition before it might easily be along with non supports recycled metal and reused present in the die casting process.
Throwpart
Die-cast part
Return to leading
Products
The two sorts of die casting equipment certainly are a hot chamber device and cold chamber machine.
Sizzling chamber die casting machine supports Hot chamber machines are used by alloys with low shedding temperatures, such as for instance zinc, jar, and lead. The temperatures essential to melt other alloys will damage the pump, which is unquestionably in direct connection with the molten metal. The requiredmetal is unquestionably found in an accesible having pot which can be into a furnace, where it really is melted to the required temp. The molten metal then runs in an attempt chamber via a great inlet along with a plunger, driven by hydraulic pressure, forces the molten metal via a gooseneck channel and within the die. Standard injection pressures to acquire a hot step die casting machine are concerning 1000 and 5000 psi. Just after the molten metal have now been inserted to the die cavity, the plunger remains down, holding stress whilst the casting confirms. After solidification, the hydraulic program retracts the plunger and the business could be ejected with the clamping unit. Prior to the injections from the molten metal, that unit closes and clamps the two halves from the die. At any time the die is attached with the die casting machine, each and every half is mounted on your big plate, known as platen. The best half the XIEJIN, the cover die, is certainly mounted to some stationary platen and aligns using the gooseneck channel. The trunk half from your die, referred to as ejector die, is mounted for your movable platen, which slides combined the tie bars. The hydraulically powered clamping unit actuates clamping bars that push this platen for the cover die and exert enough pressure to carry it closed although the molten steel is injected. Following a solidification through the metal inside the XIEJIN cavity, the clamping unit emits the die halves as well as causes the ejection system to market the casting out from the open cavity. The die can simply then be closed to be treated.
Very hotchamber machine widely open
Well-knownchamber die casting machine a substantial Opened Hot chamber machine sealed
Warmchamber die casting unit- Closed
Cold chamber expire casting machine- Cold slot provided machines are useful for other metals with good melting temperatures that could not be cast in popular chamber machines since they could damage the pumping system. This kind of alloys include aluminum, brass, and magnesium. The mandatorymolten metal may be still part of an accesible possessing pot which lies in to a furnace, where it could be melted to the mandatory temperatures. However, this holding pot could be kept separate from your expire casting machine in addition to molten alloy is ladled in the whole pot related to every casting, rather than as pumped. The metal is put in through the ladle to the shot chamber via a moving hole. The injection system on a chilly chamber machine characteristics much like regarding some hot chamber machine, nevertheless the idea is usually oriented horizontally and is not packed with a gooseneck channel. A plunger, powered by way of hydraulic pressure, forces the smelted metal with the shot slot provided and into the injection sleeve for that die. The standard injection demands for a chilly chamber expire casting machine are between 2050 and 20000 psi. Right after the smelted metal continues to be injected with your die cavity, the plunger remains forward, holding stress while the casting solidifies. After solidification, the hydraulic system retracts the plunger and the business can often be ejected from your clamping unit. Theclamping unit and mounting from your dies is identical to the chamber machine. Browse the above paragraph for features.
Chillychamber die cating unit open
Coolchamber die sending your line machine- Opened Cold slot provided die casting machine closed
Chilledchamber die casting machine a substantial Closed
Equipmentspecifications
Both popular chamber and cold chamber expire casting machines are usually portrayed from the tonnage in the clamp force they provide. The required clamp force is dependent upon basically the projected section of the parts inside the die and stress of which the molten metal is injected. Consequently , a better part will need your larger clamping force. Also, specific materials that need high injections pressures may need higher dégaine machines. How big the business must conform to many other machine specifications, such the best way shot volume, clamp stroke, lowest mold thickness, and platen proportions.
Cast parts can fluctuate greatly in proportions and so need these measures to cover up a large range. Being a outcome, die casting machines are made to each accommodate some array of this larger selection of values. Sample specifications for a variety of hot chamber and cool chamber die casting machines receive below.
Type Clamp force( ton) Max. shot volume( oz.) Clamp stroke( in.) Minutes. mold thickness( in.) Platen size( in.)
Hot step 100 74 11. 8 a couple of. 9 25 x 24
Sizzling chamber 200 116 15. almost eight 9. 8 29 x 30
Hot chamber 400 254 twenty- one. 7 11. 8 38 times 38
Cold chamber 100 35 11. 8 5. 9 twenty- three x 23
Cold chamber 4 hundred 166 21. 7 11. almost eight 38 x 38
Cold step 800 395 30. 0 12- 15. 8 55 x 55
Cool chamber 1600 1058 39. 5 19. 7 74 x 60 to 70 nine
Cold chamber 2000 1517 51. 2 25. 6 83 x 83
Come back to leading
Pedaling
The dies into which often the molten metal is inserted would be the custom tooling applied in this method. The dead are usually consists of two halves- the cover die, which often is mounted onto a immobile platen, plus the ejector XIEJIN, that is mounted as compared to movable platen. This design permits the die to actually work along its parting range. Once closed, both kick the bucket halves form an interior component cavity that is full of the molten metal to constitute the casting. This cavity is shaped by two inserts, quite cavity insert as well as the core place in, which can be inserted to the cover die and ejector XIEJIN, respectively. The cover die permits the molten metal to movement through the injection system, via a position, and to the portion cavity. The ejector die has a support plate as well as the ejector box, which could continually be mounted onto the platen and inside offers the ejection program. Right after the clamping unit separates the die halves, the clamping tavern pushes the ejector plate frontward inside ejector box which promotes the ejector pins in to the molded part, ejecting it with the core insert. Multiple a significant cavity dies are frequently used, for that your two die halves form several identical part space.
Pass awaychannels
The truth thatflow from molten metal in to the portion cavity requires several channels the fact are incorporated to the expire and differs slightly for many hot chamber machine and several cold chamber machine. In certain hot chamber machine, the smelted metal enters the die due to a piece known as sprue bushing( within the cover die) and flows in regards to the sprue spreader( inside the ejector die). The sprue describes this principal channel of molten metal starting the die. Within a frosty chamber machine, the molten alloy enters through a shot outter. After entering the die, for either form of machine, the molten metal flows through some group of runners and gets into the business cavities through gateways, which direct the flow. Typically, the cavities will contain extra space called overflow wells, which provides yet another source from molten metal during solidification. As soon as the casting cools, the smelted metal will shrink and additional material is necessary. Lastly, minor channels are included that is mainly selling the cavity towards the outdoor in the die. These programmes become venting holes allowing air to flee the die cavity. The molten material that flows through all out there channels will solidify joined towards the casting and will have to be separated readily available portion after it's ejected. A particular form of channel it generally does not detailed with material is just a trying to cool off channel. These channels allow liquid or oil to flow with the die, along with quite cavity, and remove heat through the die.
Very hotchamber die open wide
Pass awayassembly- Open
( Hot chamber) Hot chamber die sealed
Pass awayassembly- Closed
( Hot chamber) Hot chamber die increased
Pass awayassembly- Exploded perspective
( Hot chamber)
Chillychamber expire open
Pass awayassembly- Launched
( Cold chamber) Cold chamber cease to reside closed
XIEJINassembly- Sealed
( Cold chamber) Cold chamber cease to call home exploded
XIEJINassembly- Increased view
( Cold chamber)
Pass awayLayout
Along with many selections of channels, you will find additional design problems that must become considered in the sort of the dies. Firstly, the die need to permit the molten metal to flow easily into all within the cavities. Essential is normally removing the solidified casting from your die, therefore a draft angle must become put on them of the business cavity. The look inside the die should also support any complex features on the business, such as for instance undercuts, which often will demand additional die parts. Most of they put on the business cavity due to the part of the XIEJIN, and so are therefore known because slides, or side- conducts. The most frequent type of part- action is part- core allowing an excellent external undercut to get shaped. Another aspect of developing the dies is selecting the material. Dies could be fabricated away of different styles of alloys. High quality tool steel has become the typical and is usually useful for 100- 150, 500 cycles. However, steels with low carbon content tend to be more tolerant to cracking and might be sent applications for 1, 000, 000 periods. Other common materials for becomes deceased include chromium, molybdenum, nickel metals, tungsten, and vanadium. Any part- cores used in the dies may likewise be crafted from these kinds of materials.
Go back to top
Parts
Die casting typically makes using non- ferrous metals. The factfour most typical alloys the truth that are cast are exhibited below, alongside brief explanations of these properties.( Stick to the links to find the fabric library).
SuppliesProperties
Aluminiumalloys
Reduceddensity
Greatcorrosion resistance
Bigthermal and electrical conductivity
Hugedimensional stability
An easy task to solid
Needsusing a frosty chamber machine
Water pipingalloys
Hello- strength and toughness
Largecorrosion and wear resistance
Largedimensional balance
Greatestcost
Reduceddie existence as a result of high melting heat
Needsusage of a cold chamber machine
Magnesium (mg)alloys
Excessivelylow density
Hi-strength-- to- weight ratio
Outstandingmachinability after casting
Use both in hot and cold holding chamber devices
Zinc alloys
Largedenseness
Largeductility
Greatimpact power
Exceptionalsurface smoothness allowing designed for painting or plating
Demandsthis type of coating as a result of susceptibility to corrosion
Simplestto solid
May possiblyform very thin walls
Prolongeddie life because of poor melting point
Utilization of an excellent hot chamber machine
The gathering of a material for cease to reside casting is dependant on a lot of things like the density, reduction point, strength, corrosion resistance, and cost. Those items may also have an impact on the business design. An example is, the use of zinc, which is an incredibly ductile metal, enables related to thinner walls and a very far better surface finish than lots of other alloys. The fabric by no means only determines the properties from the last casting, but even impacts the device and tooling. Materials with low melting conditions, such as for instance zinc alloys, could be die-cast in a favorite chamber machine. However, materials with an increased melting temperature, this type of as aluminum and copper other metals, require the usage of cold chamber unit. Livingmelting temperature also affects the tooling, as a better temperature could have a increased adverse affect on living through the dies.
Come back to premier
AchievableDefects
ProblemCauses
Screen
Injectionspressure too much
Holdforce lacking
Bareportions
Inadequateshot volume
Slowertreatment
Lowerpouring temperature
Pockets
Remedytemperature excessive
Not- clothes cooling charge
Very hottearing
Reduced- uniform cooling rate
Ejector marks
Air conditioningtime too brief
Dispositionforce excessive
Many to sum up defects are induced by way of a non- clothes cooling rate. A significantvariation within the cooling rate will get brought on by non- clothes wall thickness or non a substantial uniform die temperature.
Come back to premier
StyleRules
Highestdivider fullness
Reduce the maximum divider thickness of account to limit the cycle time( injection time frame and cooling time specifically) and reduce steadily the part volume
Inappropriate
Spend thick walls
Partwith thick walls
Proper
Partredesigned with thin walls
Partredesigned with thin walls
Outfitswall thickness will assure homogeneous cooling and minimize disorders
Drastically wrong
No- uniform wall fullness
No- uniform wall fullness( t1≠ t2)
Correct
Homogeneous wall thickness
Standardwall fullness( t1= t2)
fourcorners
Sportcorners to cut back stress union and fracture
Interiorradius has to be at the very least the thickness within the partitions
Wrong
Sharpenedpart
Sharpenedpart
Right
Roundpart
Roundpart
Set up
Apply an excellent draft angle to any or all surfaces parallel for the parting road to facilitate removing the business from your die.
Aluminum: 1° for walls, 2° for interior callosité
Magnesium: 0. 75° meant for walls, 1. 5° for interior callosité
Zinc: 0. 5° meant for walls, 1° for inside induration
Completely wrong
Simply noDraft Angle
Hardly any draft angle
Right
WritePosition
Writeangle( q)
Undercuts
Reduce the quantity of external undercuts
Outsideundercuts require side- cores which will raise the tooling cost
Some fundamental external undercuts could be solid by relocating the parting collection
Basicexternal undercut
Basicexterior undercut
XIEJINcan't separate
Expire can't individual
Brand newparting collection allows undercut
Brand newparting collection allows undercut
Upgradinga characteristic can remove another undercut
Elementwith hinge
Spend in your
Jointrequires side- primary
Jointrequires side- primary
Remodeledhinge
Re-designedhinge
Refreshinghinge could be cast
Refreshinghinge may be cast
Sign up for all internal undercuts that want lifters- Jamming of these kinds of devices often only occurs in XIEJIN casting
Developinga job inside the part of part may allow a side- primary to make an internal undercut
Internalundercut accessible from the side
Interiorundercut accessible
from the side
Decoratinga component can remove an excellent internal undercut
Spend inner undercut
Spend the internal undercut
Pass awaycan't separate
Pass awayaren't able to separate
Portionredesigned with video slot
Portionredesigned with slot
Refreshingpart might be cast
Brand newinside your could be solid
Minmisevolume of side- action guidelines
Addedside- action guidelines will limit the amount in possible cavities inside the XIEJIN
Come back to best
ExpenseMotorists
Substancecost
The material cost is unquestionably dependant on the load from fabric that's needed is and the machine price to the fact that material. The of textile is clearly a be a consequence of the business volume and subject material density, however, the business 's maximum wall thickness can may also may play a role . The of fabric the fact that's needed is includes the info that fills the channels from your die. Way ofspend thinner walls will need your larger way of channels to make certain that the sum total part fills quickly and consistently, and so will boost the total amount of required material. Alternatively , this additional material is normally less than the amount info saved with the decrease in portion volume, a direct result leaner walls. Therefore, despite the more channels, using thinner walls can typically lower the items expense.
Manufacturingexpense
The availability expense is principally calculated from the with an hourly basis rate as well as the cycle time frame. How big ishourly rate is proportionate to how big is the die casting machine being applied, so you should understand how the business design influences machine selection. Die casting items are usually through the tonnage from the clamping push they supply. The mandatory clamping force is determined by the projected precise location of the part plus the stress of which the molten material is injected. Therefore, a better part will demand a better clamping force, thus a extra expensive machine. Also, certain supplies that want high injection challenges may necessitate higher tonnage equipment. The magnitude of15356 part must too conform to other machine requirements, such as for example clamp stroke, platen size, and shot capacity. Plus the size of the device, the sort of machine( hot step vs. cold chamber) might also influence the fee. The use from materials with good melting temperature ranges, exactly like aluminum, will demand cool chamber machines that are ordinarily higher priced.
The cycle time period may be divided inside the injection time, cooling period of time, and resetting time. By reducing some of these times, manufacturing cost will undoubtedly be decreased. The businessinjection time will get decreased by reducing the maximal wall thickness in the business. Too, certain materials might be injected faster than others, even so the injection instances are incredibly short the truth that expense saving are negligible. Substantial period may be saved with a hot chamber machine for the reason that in cold chamber machines the molten metal must certanly be ladled into the device. This ladling time depends inside the shots weight. They might requirecooling time is unquestionably also decreased for lower wall membrane thicknesses, as they might need fewer time and energy to cool throughout . Several thermodynamic property of the fabric also influence the cooling time. Lastly, the resetting time is determined by the equipment size as well as the component size. A more substantial part can require larger motions from the equipment to spread out, close, and eject the business, and a larger machine requires more hours to execute these operations. Also, the usage of any side- cores can slow this process.
Pedalingcost
The tooling cost has two key parts- the die established as well as the machining from the cavities. The price of the die set is principally maintained by the size the business 's envelope. A more substantial part requires a larger, higher priced, XIEJIN set. The expense of engineering the cavities is influenced by simply almost every facet of the business 's geometry. The main expense driver certainly is the size of the cavity that really must be made, measured with the projected precise location of the cavity( corresponding to the projected section of the part and projected holes) and its particular depth. Any elements that will demand additional engineering time will enhance the cost, such as the feature depend, parting surface, side- induration, tolerance, and surface roughness.
The amount of parts and materials used will impact the tooling life and for that reason impact the fee. Materials with good spreading temperatures, such as for instance copper, could cause a quick tooling lifestyle. Zinc, which might be ensemble at lower temperatures, allows to acquire a considerably longer tooling lifestyle. This effect becomes more to expensive with higher production quantities.
An individual final consideration is the quantity of side- action guidance, that may indirectly impact the cost. The additional expense to have side- cores is identified by exactly how many to be used . However, the quantity in directions can restrict the total amount of cavities that will become in the die. As an example, the die to obtain a part which needs 3 side- core guidance can just only contain 2 major. There's absolutely no direct expense added, but most likely the usage of more cavities may possibly provide further savings.